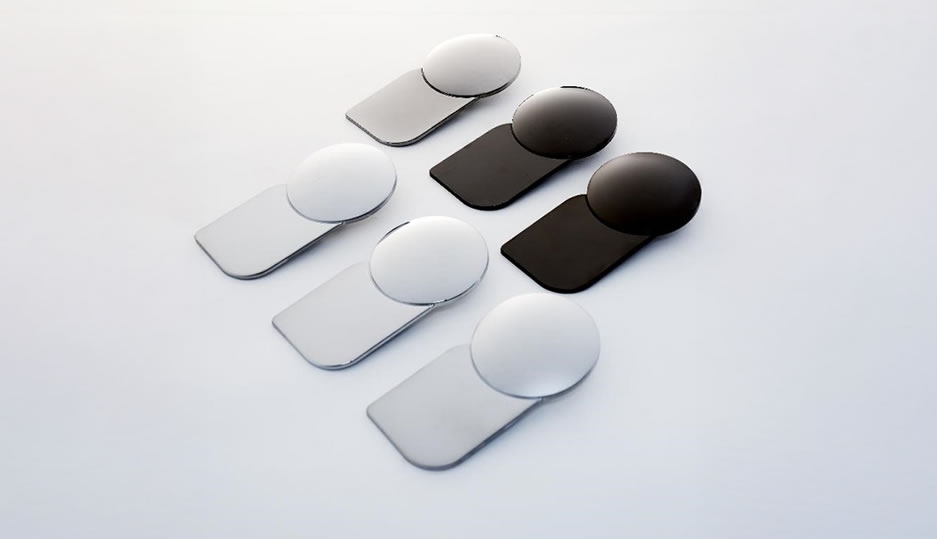
Alan Gardner
Chrissy Pullara
O revestimento de cromo ainda é a escolha preferida para muitas aplicações de acabamento em metais e plásticos. A demanda pelo acabamento brilhante e lustroso, com característico toque ‘frio metálico’ do cromo, continua a diferenciar os produtos que o tem, mesmo apesar da concorrência de outros acabamentos, como revestimentos orgânicos e deposição a vapor (PVD). O cromo resistiu aos desafios competitivos devido à sua estética incomparável, bem como às suas capacidades técnicas superiores, incluindo desempenho excepcional contra corrosão, capacidade de revestimento em múltiplos substratos e fatores ligados à cadeia de suprimentos, como escala industrial, base extensa de aplicadores instalados e longa história e experiência de aplicação. O cromo é amplamente utilizado na indústria de acabamento de metais, tanto para revestimentos decorativos quanto para revestimentos de cromo duro.
O revestimento de cromo é utilizado comercialmente desde meados de 1924. Em aplicações decorativas, o cromo é depositado como uma fina camada (0,25–0,8 µm) sobre o níquel, fornecendo um depósito econômico e altamente resistente à corrosão. Os depósitos de cromo decorativo são produzidos usando eletrólitos de cromo trivalente e hexavalente. Na última década, processos baseados em cromo trivalente têm ganhado crescente preferência na indústria, impulsionado pela Reach (Registration, Evaluation, Authorization and Restriction of Chemicals, da União Europeia) e sua integração com economia circular e sustentabilidade.
O cromo brilhante pode ser aplicado como camadas contínuas (regulares) ou descontínuas. Depósitos descontínuos são formados depositando o cromo sobre camadas de níquel microporosas (ou microfissuradas, hoje em desuso). A escolha de uma camada contínua ou descontínua depende do nível necessário de resistência à corrosão. A falha do revestimento de cromo brilhante é frequentemente relacionada ao desenvolvimento de microcavidades profundas como resultado da corrosão iniciada em fissuras ou poros aleatórios na superfície da camada de cromo.
A corrosão é um mecanismo eletroquímico. Como essas fissuras ou poros estão relativamente espaçados, a corrente desenvolvida pelo par cromo/níquel se concentra em alguns pontos; microcavidades mais profundas se formam nesses pontos e penetram rapidamente através do depósito de níquel e do substrato do componente base ou camadas menos nobres, usualmente constituídas de cobre. Induzir microdescontinuidades (microfissuras ou microporos) na superfície distribui a ‘corrente de corrosão’ e reduz a taxa de corrosão. Tipicamente, artigos revestidos para a ‘condição de uso 1 e 2’ (ambiente de baixa exposição à corrosão, exemplo: interiores secos) usariam revestimento de cromo regular, enquanto o revestimento para a ‘condição de uso 3’ (ambientes mais agressivos, como exteriores expostos a umidade, chuva, sal e produtos químicos), ou superior, usaria uma camada descontínua (segundo a norma ASTM B456 - American Society for Testing and Materials).
Processo de Eletrólitos Decorativos de Cromo Hexavalente
São comumente utilizados quatro tipos de eletrólitos de cromo hexavalente:
- Catalisadores apenas de sulfato;
- Catalisadores de sulfato-fluoreto;
- Catalisadores de sulfato-fluoreto-orgânico;
- Alta velocidade autorreguladora (SRHS).
As principais diferenças entre os sistemas são delineadas na Tabela I.
TABELA I — Sistemas de Eletrolíticos de Cromo Hexa Decorativo
Atualmente, os eletrólitos mais comuns empregados são baseados no catalisador duplo sulfato-fluoreto. Esse catalisador misto tem as vantagens de melhorar a eficiência do cátodo, o poder de cobertura e a capacidade de revestir camadas de níquel brilhante quando comparado ao catalisador de sulfato puro.
Ao longo da última década, a popularidade do sistema de catalisador triplo cresceu. Esse sistema tem características semelhantes ao catalisador duplo, com as vantagens de eficiências catódicas mais altas, uma janela operacional mais ampla e um poder de cobertura aperfeiçoado. Para operar esses sistemas, é necessária a análise regular das concentrações de ácido crômico, ácido sulfúrico e catalisadores proprietários.
Em mercados nos quais o acesso ao controle analítico regular é limitado, o uso de produtos químicos SRHS continua (SRHS são Substâncias que Suscitam Elevada Preocupação; identificadas pela Agência Europeia dos Produtos Químicos - ECHA). Esses sistemas regulam a proporção dos níveis de sulfato ativo e catalisador para o ácido crômico por meio do uso de agentes solubilizantes proprietários.
Os banhos com cromo hexavalente têm uma distribuição de camadas pobre. Portanto, para revestir de acordo com a especificação, é necessário calcular o tempo de eletrodeposição com base nas espessuras mínimas exigidas em superfícies significativamente mais ‘expostas’ aos anodos. Um fator importante no tempo de eletrodeposição é a eficiência catódica das soluções de cromo, que é influenciada pelos seguintes fatores:
- Tipo de eletrólito (Descritos na Tabela I)
Soluções com eficiências de cátodo mais altas têm poder de deposição e cobertura melhores em comparação com os eletrólitos mais simples. - Concentração da solução
A eficiência catódica de uma solução cresce à medida que a concentração de ácido crômico aumenta até atingir um pico, em cerca de 250 g/L; depois disso, qualquer elevação na concentração diminui a eficiência catódica. Soluções de alta concentração são, no entanto, mais simples de controlar do que as de baixa concentração, pois são menos afetadas por pequenas mudanças no teor de sulfato e operarão com um teor de óxido mais alto; usualmente, são utilizadas para ter maior estabilidade em processos com alta taxa de arraste. - Densidade de corrente empregada
A eficiência catódica varia diretamente com a densidade de corrente: quanto maior a densidade de corrente, maior a eficiência catódica. - Temperatura da solução
A eficiência catódica diminui com o aumento da temperatura. No entanto, temperaturas operacionais mais altas permitem o uso de densidades de corrente mais altas. Na prática, a temperatura ideal está relacionada à densidade de corrente empregada. Com soluções autorreguláveis, um aumento na temperatura resulta em um ligeiro aumento na eficiência catódica. - Composição da solução
A eficiência catódica também é afetada pelo conteúdo de cromo trivalente e contaminações como ferro e níquel (contaminantes mais comuns). A eficiência da solução diminui à medida que esses contaminantes se acumulam na solução. A eficiência catódica também é reduzida se a solução estiver desequilibrada, por exemplo, quando os elementos da solução estão abaixo ou fora da relação ideal.
Cálculo dos Tempos de Eletrodeposição
Qualquer mudança na densidade de corrente, geralmente, envolve um ajuste correspondente na temperatura para manter a solução dentro da faixa ideal de eletrodeposição. Essas mudanças também afetarão a eficiência catódica.
A Tabela II mostra o tempo necessário para produzir um depósito com espessura média de 1 µm em várias faixas de eficiências catódicas e densidades de corrente. Esses tempos de eletrodeposição são para valores médios de espessura sob condições de densidade de corrente uniforme. Na prática, haverá uma variação considerável na densidade de corrente na superfície das peças e, portanto, a espessura média do cromo aplicado estará acima de quaisquer requisitos de espessura mínima.
TABELA II — Tempo de Eletrodeposição (Min) para um Depósito Médio de Cromo de 1-µm
Equipamento e anodos
As soluções de banhos de cromo geralmente são contidas em tanques revestidos de PVC – PVDF. A solução é aquecida por meio de aquecedores elétricos de imersão, revestidos de sílica, Teflon, serpentinas de vapor ou água quente. Anodos de liga de estanho-chumbo são geralmente empregados para a eletrodeposição de cromo hexavalente.
Em um tanque de banho de cromo, os anodos de chumbo servem a dois propósitos: como eletrodo positivo e para manter a solução em equilíbrio satisfatório, reoxidando o cromo trivalente em ácido crômico. A área do anodo deve ser cerca de 20% maior do que a área da carga normal de galvanoplastia. Quando a corrente está passando pela solução de cromo ocorrerá gaseificação nos anodos, que normalmente são cobertos com um filme de cor chocolate escuro. Esse filme é necessário para garantir que o cromo trivalente produzido pela redução eletroquímica do ácido crômico no cátodo seja reoxidado para garantir o equilíbrio correto da solução.
Controle de névoa
Durante a eletrólise do ácido crômico, é produzida uma névoa que deve ser controlada pelo uso de um supressor químico adequado, geralmente em conjunto com extração através de sistema de exaustão. Os supressores de névoa químicos mais comuns são geralmente baseados em sulfonatos de perfluorooctano (PFOS). No entanto, esses materiais estão se tornando objeto de proibição devido à sua persistência ambiental e efeitos bioacumulativos em mamíferos.
A eliminação do PFOS tem sido um tópico sensível para a EPA (Environmental Protection Agency, a Agência de Proteção Ambiental dos Estados Unidos), bem como para agências estaduais e locais e estações de tratamento de esgoto de propriedade pública dos EUA.
Felizmente, substitutos comercialmente viáveis estão disponíveis para uso em soluções de ácido crômico. Essas alternativas, sem PFOS, são compatíveis com os regulamentos da EPA e podem controlar de forma consistente e confiável a emanação de névoa em banhos de cromo.
Manutenção da solução
As soluções de banho de cromo são regularmente analisadas: ácido crômico, sulfatos, catalisadores e contaminantes. A deficiência na concentração de ácido crômico é corrigida pelo uso de uma mistura de sal proprietária que restaura o equilíbrio dos catalisadores da solução e cromo ao mesmo tempo. A deficiência de sulfato é restaurada por adições de ácido sulfúrico. Se os sulfatos estiverem muito altos devido ao arraste da etapa anterior de eletrodeposição de níquel, a concentração é reduzida pela adição de carbonato de bário.
Para a operação correta, é desejável que uma pequena concentração do cromo (1–3 g/L) deva estar presente na solução como cromo trivalente. Acima desse nível, a eficiência da solução pode cair e mostrar um revestimento de cromo com menor poder de cobertura. Com o tempo, as contaminações metálicas, como ferro, cobre ou níquel, se acumularão na solução. Esses metais pesados são frequentemente determinados analiticamente como ‘óxidos’ (Cr2O3, Fe2O3, etc.). Os óxidos totais não devem ultrapassar 5% da concentração total de hexavalente.
Processos à Base de Cromo Trivalente Decorativo
As soluções de cromagem trivalente são uma alternativa cada vez mais empregada na indústria de acabamento de metais por uma variedade de razões, incluindo aumento da eficiência catódica e poder de penetração, menor toxicidade, ausência de compostos com PFOs e PFA (perfluoroalcoxi). A concentração total de metal de cromo usada no banho de cromo trivalente é significativamente menor do que a de uma solução de cromo hexavalente – menos de 20 g/L para banhos de cromo no processo trivalente.
Essa redução na concentração de metal, além de menor viscosidade da solução, ocasiona menor arraste e, por consequência, menor tratamento de águas residuais; portanto, uma redução de custos no processo de cromagem. Os banhos de cromo trivalente, como resultado de seu excelente poder de penetração, também produzem menos rejeições e permitem maiores cargas em área nas gancheiras em comparação com o cromo hexavalente. Embora a cromagem trivalente apresente várias vantagens, o sistema também possui uma desvantagem: especificamente, é difícil alcançar a mesma cor de um depósito de cromo hexavalente na mesma taxa de deposição ao utilizar um eletrólito de cromo trivalente.
Os sistemas de cromo trivalente atuais fornecem uma cor praticamente igual à do cromo hexavalente, a uma taxa de deposição mais lenta, ou uma cor ligeiramente mais escura, a uma taxa de deposição comparável à do cromo hexavalente.
Assim como existem diferentes opções de eletrólitos para a cromagem com cromo hexavalente, existem escolhas semelhantes para a cromagem com cromo trivalente. Os processos de cromo trivalente utilizam um eletrólito à base de sulfato ou cloreto. Uma comparação desses sistemas pode ser vista na Tabela III.
Tabela III — Comparação dos Sistemas Decorativos de Cromo Trivalente
Sistemas à base de sulfato depositam um revestimento de maior pureza, o que leva a uma melhor proteção contra corrosão e uma cor mais próxima do cromo hexavalente. A química dos sistemas à base de sulfato também é menos corrosiva, o que evita a deterioração do ambiente de revestimento e das áreas não revestidas dos componentes.
Os sistemas à base de cloreto são capazes de depositar revestimentos a uma taxa semelhante à do cromo hexavalente. No entanto, a cor é tipicamente mais escura do que a do cromo hexavalente devido aos aditivos necessários para atingir a rápida taxa de deposição. Os sistemas de cloreto também utilizam anodos de grafite (carbono), que são mais baratos do que os anodos de titânio revestidos (MMO) necessários para operar os sistemas trivalentes à base de sulfato.
Equipamento e Manutenção de Solução
As soluções de eletrodeposição de cromo trivalente operam com equipamentos semelhantes aos usados com os processos de níquel brilhante.
As soluções de cromo trivalente devem ser instaladas em tanques revestidos com PVC ou polipropileno. Devem ser usadas serpentinas de titânio, ou aquecedores de imersão elétrica revestidos de titânio, sílica ou Teflon. Recomenda-se filtração contínua, e anodos de grafite (alta compactação) – preferencialmente cilíndricos ou titânio revestido – MMO, são necessários dependendo da química base (cloreto ou sulfato).
A análise do banho de revestimento envolve a avaliação regular das concentrações de cromo, sal condutor e complexante, tensão superficial, bem como pH e gravidade específica. A dosagem por ampere-hora dos componentes de reposição deve ser utilizada para facilitar a operação. Contaminantes devem ser controlados para maior estabilidade de processo e cor.
Revestimentos Trivalentes Escuros
Revestimentos escuros estão se tornando cada vez mais utilizados nas indústrias. A aparência de um acabamento escuro e brilhante, que pode suportar os critérios de testes do cromo hexavalente, é desejada para muitas aplicações, e soluções de cromo trivalente escuro existem e atendem tanto aos requisitos de aparência quanto técnicos. Muitas OEMs incorporaram esses acabamentos em suas especificações.
Essas soluções exibem excelente cobertura, poder de penetração e cor consistente, em uma ampla faixa de densidades de corrente, além da vantagem de operação com baixo teor de metal em comparação com o cromo hexavalente. Esses revestimentos, após aplicação de passivadores de camadas de cromo tri, são capazes de superar 96 horas de teste de névoa salina com ácido acético, acelerado por cobre (CASS), sem mudança notável na aparência do depósito. Esses revestimentos também têm uma vantagem sobre o cromo hexavalente por serem resistentes à corrosão por cloreto de cálcio, ou ‘lama russa’.
Os processos de cromo trivalente têm a necessidade de receber uma passivação superficial do depósito, também chamada de ‘pós-dip’, que vai promover a formação de óxidos estáveis responsáveis pela resistência à corrosão dos processos. Há tecnologias de passivação com atributos de simulação de ensaios de corrosão antevendo resultados demorados de corrosão acelerada, como NSS (Neutral Salt Spray - Névoa Salina Neutra) ou CASS (Copper Accelerated Acetic Acid Salt Spray - Névoa Salina com Ácido Acético e Cobre).
Revestimento de Cromo Duro
O revestimento de cromo duro é normalmente descrito como a aplicação de um depósito de cromo eletrodepositado com uma espessura superior a 5 micra. Os depósitos de cromo duro são normalmente revestidos com uma espessura de 5 a 250 micra, embora, em teoria, possam ser alcançadas espessuras quase ilimitadas.
O revestimento comercial de cromo duro começou no final da década de 1920 para o início da década de 1930 após trabalhos nos EUA e na Alemanha usando um banho baseado em ácido crômico e ácido sulfúrico em uma proporção de 100:1. Nos anos seguintes, a formulação básica do banho de eletrodeposição para revestimento de cromo duro não foi alterada e, embora tenha havido melhorias na tecnologia, muitos galvanizadores ainda usam essa química original.
A razão para o crescimento do revestimento de cromo duro em um negócio multimilionário é que o depósito de cromo dessas soluções possui uma combinação de propriedades que não foram igualadas por nenhuma das tecnologias posteriores oferecidas e testadas, algo que tem acontecido até últimos anos, visto o que se passa na Europa com a dificuldade de banimento deste processo por ausência de tecnologias com tecnologia e custo benefícios viáveis.
Essas propriedades incluem:
- Alta dureza;
- Baixo coeficiente de fricção;
- Excelente resistência ao desgaste;
- Excelente resistência à corrosão (especialmente em atmosferas oxidantes).
O cromo duro pode ser aplicado a um custo muito baixo em comparação com suas alternativas, e pode ser revestido em uma ampla variedade de substratos. Isso explica por que, apesar das questões ambientais, o cromo duro continua a ser amplamente especificado e utilizado.
A capacidade de eletrodepositar metal de cromo de uma solução de cromo hexavalente teoricamente não é possível; no entanto, é alcançada usando um radical ácido como catalisador. Este catalisador, historicamente, tem sido sulfato, embora outros, como fluoreto, também possam ser usados.
Tipos de Cromo Duro
Existem três tipos principais de cromo duro em operação. As propriedades desses sistemas são apresentadas na Tabela IV.
Tabela IV — Comparação de Sistemas de Cromo Duro
Processos catalisados por fluoreto são usados com sulfato. Eles produzem um depósito muito mais duro quando depositados e têm uma eficiência catódica muito maior do que a solução Sargeant, resultando em uma taxa de deposição mais alta.
Os processos catalisados por flúor são usados com sulfato. Eles fornecem um depósito muito mais duro quando galvanizados e têm uma eficiência catódica muito maior do que a solução Sargeant, e, assim, têm uma taxa de deposição mais alta. O lado negativo é que a sua química é muito mais agressiva, tanto para os equipamentos quanto para as peças galvanizadas, portanto, a contaminação metálica é um problema sério. Isso limitou seu uso, embora tenham encontrado algumas aplicações específicas onde são usados extensivamente.
Sais de ácidos orgânicos também podem ser usados em conjunto com sulfato nas soluções de cromo, e se tornaram, para a maioria, a opção preferida. Eles têm alta eficiência, depositam camadas muito duras e, devido à alta densidade de microfissuras encontradas nesses sistemas, oferecem boa proteção contra corrosão. Alguns dos sistemas mais antigos usados têm um efeito negativo na taxa de corrosão do anodo, mas as químicas mais modernas mostram corrosão do anodo semelhante aos primeiros processos de Sargeant.
Equipamento
As soluções de galvanização com cromo duro devem ser usadas em tanques revestidos com PVC. Tanques revestidos com chumbo não são recomendados.
Qualquer equipamento de aquecimento ou resfriamento necessário deve ser construído de PTFE ou um fluorocarbono similar, tântalo ou titânio; embora o uso de titânio não seja recomendado se estiver usando um processo catalisado por flúor.
A energia usada para a galvanização com cromo duro deve ter uma onda filtrada (ripple < 5%), porque a ondulação pode causar muitos problemas técnicos em uma solução de cromo duro. As fontes de alimentação devem ser capazes de até 15 V para aplicações normais. Como grandes correntes e tensões são usadas, as barras condutoras devem ser capazes de transportar a corrente necessária sem superaquecer. Também é importante isolar todos os materiais condutores da energia externa para reduzir o risco de formação de correntes dispersas.
Para a maioria dos sistemas, é recomendada a utilização de anodos de estanho-chumbo (7% de Sn). A área do anodo deve ser cerca de 150% da área do cátodo para reduzir o risco de aumento da concentração de cromo trivalente.
Em algumas circunstâncias, anodos de chumbo/antimônio são usados, pois são mais rígidos do que os de estanho/chumbo e, portanto, são menos propensos a ‘entortar’ em tanques maiores. Esses anodos não devem ser usados com sistemas à base de flúor, porque corroem mais rapidamente e têm uma condutividade menor do que os anodos tradicionais de estanho/chumbo.
Em alguns casos específicos, anodos de titânio revestidos de platina estão sendo usados. Inicialmente, eles custam substancialmente mais, porém, muitas vezes economizam dinheiro, pois podem durar até 10 anos e não geram lodo de cromato de chumbo, que pode ser difícil de remover. É importante, ao usar esses anodos, manter uma pequena quantidade de chumbo na solução; sem isso, a concentração de cromo trivalente pode aumentar, levando a problemas de qualidade.
Devido ao baixo poder de cobertura das soluções de eletrodeposição com cromo duro, o uso de anodos auxiliares e máscaras é comum, e constitui uma das principais habilidades necessárias para os galvanizadores de cromo duro.
Equipamentos de exaustão são necessários porque a eletrodeposição com cromo duro é muito ineficiente do ponto de vista eletroquímico e gera uma quantidade considerável de gás hidrogênio no cátodo.
Isso irá produzir uma ‘névoa’ muito pesada saindo do banho. Os limites de exposição permitidos foram recentemente reduzidos e são muito baixos; por essa razão, é muito importante fornecer uma excelente extração. Também é possível usar surfactantes para reduzir a tensão superficial do tanque de eletrodeposição.
Operação
A operação de uma solução de cromo duro não é complexa, mas há certos aspectos que devem ser controlados. São eles: concentração de ácido crômico, concentração de sulfato, concentração de catalisador (se estiver usando mais do que sulfato), temperatura e contaminação por óxidos metálicos, como ferro, níquel, cobre ou cromo trivalente; isso é importante para garantir a melhor eficiência da solução de galvanização (veja a seção sobre contaminação).
Substratos
É possível galvanizar a maioria dos substratos com cromo duro alterando o pré-tratamento utilizado. Os substratos comumente galvanizados incluem aço, aço temperado, ferro fundido, bronze (usado como subcamada para fornecer proteção contra corrosão) e alumínio. É vantajoso usar um banho catalisado por flúor ao galvanizar aços temperados, ou ligas de níquel, se a ativação por imersão ou anódica estiver sendo usada, mas é possível galvanizar esses substratos nos outros sistemas catalisados usando ativação separada e uma ativação catódica.
Também é possível eletrodepositar cromo duro sobre cromo duro previamente galvanizado ou outros acabamentos eletrodepositados. Um deles é o níquel químico, onde uma combinação do desgaste e dureza do cromo duro com a espessura uniforme do níquel químico vai proporcionar muitas vantagens.
Contaminação
Todas as soluções de cromo acumulam contaminantes, e é importante minimizá-los, pois têm um efeito negativo na qualidade da galvanização. Isso é mais notado na eletrodeposição de cromo duro do que com o cromo decorativo, pois há um arraste mínimo de banhos de cromo duro e, portanto, os contaminantes tendem a aumentar mais rapidamente nessas soluções.
À medida que os cátions se acumulam na solução de galvanização, eles reduzem a condutividade da solução, levando a um aumento na tensão necessária para manter uma densidade de corrente e a uma possível perda de eficiência.
Propriedades
O cromo duro oferece um revestimento duro, deslizante, resistente à corrosão e ao desgaste. Uma das principais razões para seu bom desempenho em testes de corrosão é que o depósito é microfissurado; se o depósito for espesso o suficiente (normalmente > 25 micra), as fissuras no depósito não atingem o substrato e o desempenho contra corrosão é visivelmente melhorado.
As macrofissuras, por outro lado, podem resultar em corrosão acelerada. Geralmente, se um depósito é macrofissurado, ele não é tão duro nem tão resistente ao desgaste quanto um processo microfissurado. A microfissuração também é vantajosa em aplicações lubrificadas, pois o lubrificante é armazenado nas fissuras. A Tabela V apresenta um resumo de algumas das características de desempenho dos depósitos de cromo duro.
Tabela V — Características de Desempenho dos Depósitos de Cromo Duro
Artigo originalmente publicado na Products Finishing: www.pfonline.com/articles/chromium-plating
Tradução: Carmo Leonel Júnior