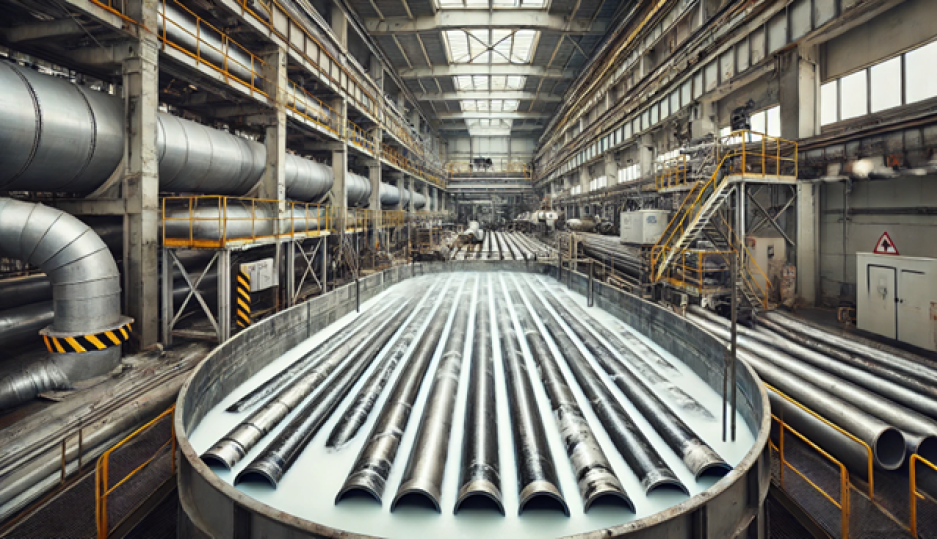
Leonardo Fassio
Coordenador AT na SustenTS - Quimidream, Especialista em camadas
de conversão para pré-pintura e conformação a frio
A importância de ações sustentáveis nos processos de aplicação de camada de conversão, destacando práticas inovadoras e benefícios a longo prazo para o meio ambiente e para a indústria.
1. Introdução
A sustentabilidade tem se tornado um dos temas mais relevantes no cenário industrial moderno, especialmente em setores que tradicionalmente causam impacto significativo ao meio ambiente. Esse conceito, embora relativamente recente para muitos, já era discutido há mais de 300 anos por Hannß Carl von Carlowitz, em sua obra ‘Instrução de Arboricultura Selvagem’, onde abordava a necessidade de um uso responsável dos recursos naturais diante da ameaça de esgotamento das florestas na Saxônia, Alemanha, devido à mineração. Naquela época, a extração intensiva de madeira para atender à indústria de mineração resultou em uma grave crise ambiental, evidenciando a importância de práticas sustentáveis.
A crescente preocupação com a sustentabilidade tem impulsionado mudanças significativas nos processos industriais, especialmente nas indústrias que lidam com produtos químicos, como com o processo de fosfatização, amplamente utilizado para preparar superfícies metálicas para pintura e revestimento, oferecendo proteção contra corrosão e melhorando a adesão de tintas e outros revestimentos ou utilizado como lubrificante redutor de atrito. Os impactos ambientais desses processos tradicionais são motivo de atenção, uma vez que envolvem o uso de substâncias químicas potencialmente poluentes, como metais pesados e fosfatos.
Diante disso, a implementação de ações efetivas para tornar esses processos mais sustentáveis tem se tornado um objetivo essencial para a indústria moderna. Estratégias como a substituição de produtos químicos nocivos, a reciclagem de resíduos e a otimização do consumo de energia são apenas algumas das abordagens que vêm sendo adotadas para reduzir os impactos ambientais da fosfosfatização. Essas ações não apenas minimizam o impacto ambiental, mas também representam vantagens competitivas e econômicas, refletindo a responsabilidade social e ambiental das empresas.
Este artigo busca explorar a importância dessas ações sustentáveis nos processos de aplicação de camada de conversão, destacando práticas inovadoras e benefícios a longo prazo para o meio ambiente e para a indústria. Ao analisar a adoção dessas práticas, pode-se compreender como uma abordagem sustentável consegue ser integrada ao cotidiano industrial, reforçando a relevância da responsabilidade ambiental em processos químicos complexos.
2. Por que não misturar os efluentes
A importância de não misturar efluentes nos processos de tratamento de superfícies está diretamente relacionada à sustentabilidade, à eficiência energética e à viabilidade econômica da reciclagem ou destinação desses efluentes.
Quando misturamos diferentes substâncias residuais, como óleos, sais, metais e outros compostos, ocorre um aumento significativo da entropia do sistema. Esse conceito, conforme a Segunda Lei da Termodinâmica, estabelece que a entropia seja aumentada. Resumindo: sistemas tendem naturalmente ao estado de maior desordem a menos que se realize um trabalho de reversão dessa entropia, fornecendo uma quantidade considerável de energia para reverter esse estado.
Em processos industriais, especialmente os que envolvem efluentes, a separação dos componentes misturados se torna um desafio técnico e econômico devido ao custo para superar as forças intermoleculares e reorganizar as substâncias de maneira a facilitar o reaproveitamento ou o descarte seguro. Esse processo de separação exige recursos energéticos e financeiros elevados, o que muitas vezes torna a reciclagem economicamente inviável.
A sustentabilidade dos processos industriais depende, portanto, da capacidade de controlar e evitar a mistura desordenada e indiscriminada de efluentes desde o início. Ao manter esses resíduos organizados e separados, o tratamento subsequente torna-se mais eficiente e menos dispendioso, possibilitando a reciclagem ou destinação de forma ambientalmente correta e com menor impacto econômico. Assim, evitar a mistura dos efluentes reduz a necessidade de tratamento intensivo, diminuindo a geração de resíduos destinados ao descarte.
Dessa forma, ao priorizar a organização e a segregação dos efluentes na origem, as indústrias podem contribuir para processos mais sustentáveis e menos impactantes ao meio ambiente, promovendo o reaproveitamento de recursos e a redução de custos operacionais em um ciclo mais eficiente de economia circular.
3. Reciclagem de banhos desengraxantes
Etapa essencial no processo de preparação de superfícies, o desengraxe visa remover sujeiras acumuladas ao longo das etapas produtivas anteriores, principalmente resíduos orgânicos, como óleos, graxas, ceras e restos de pastas de estampagem. Em alguns casos, também pode ser necessário remover contaminantes inorgânicos, como cavacos metálicos ou sais resultantes de processos químicos anteriores. O objetivo principal é garantir a eliminação total de qualquer impureza que possa comprometer a integridade da superfície, preparando-a para a aplicação de uma camada de fosfato de zinco de forma eficiente e sem problemas.
Um dos principais desafios enfrentados no desengraxe é a saturação do banho desengraxante. Com o uso contínuo, os contaminantes orgânicos acabam sendo emulsionados, o que leva ao esgotamento do banho e exige sua substituição. A frequência dessa troca depende tanto do volume de produção quanto do nível de contaminação das peças, mas é inevitável que ocorra, o que gera altos volumes de efluentes a serem tratados, além da necessidade de mais água e produtos químicos para manter a operação de desengraxe.
Atualmente, o mercado disponibiliza diversas formulações de desengraxantes químicos, compostas, em geral, por agentes inorgânicos, que realizam a saponificação de óleos e graxas, e agentes orgânicos (surfactantes), responsáveis por assegurar a limpeza detalhada da superfície. No entanto, esses compostos orgânicos tendem a formar emulsões, contribuindo para a saturação do banho.
Por meio de Pesquisa & Desenvolvimento, já é possível reciclar esses banhos desengraxantes com a adição de agentes demulgantes, substâncias que quebram as emulsões presentes no banho, possibilitando a recuperação da água e dos compostos inorgânicos. Assim, somente os agentes orgânicos precisam ser repostos para dar continuidade ao processo.
Para realizar a operação de reciclagem, o agente demulgante é adicionado ao banho na proporção de 0,1 a 1,0% de seu volume, e o tempo necessário é aguardado para a separação de fases. A parte sobrenadante é removida, a solução é completada novamente e são adicionados os surfactantes necessários para retomar a operação de limpeza. Dependendo da estrutura de instalação, essa reciclagem pode ser feita de forma contínua, proporcionando maior eficiência e economia ao processo.
4. Inibidores eficientes de corrosão ácida
Na maioria dos processos de aplicação de camadas de conversão, a decapagem ácida é o método mais utilizado para a remoção de óxidos e carepas, proveniente do processo de produção do aço e/ou tratamentos térmicos anteriores. Essas carepas, apesar de muito aderentes, devem ser removidas de toda a superfície a ser convertida, pois uma de suas características é ser altamente microfissurada, inibindo a fosfatização e podendo se desplacar durante o processo de conformação, por exemplo, causando diversos problemas, como falta de lubrificação na região.
A carepa, normalmente, é formada por diferentes camadas de óxidos, e a composição e espessura dela variam bastante, dependendo do tempo, temperatura de exposição, composição do aço, composição da atmosfera e agressividade da deformação à quente que foi realizada.
Geralmente, a composição da carepa se dá da seguinte forma: primeiramente, uma camada externa mais rica em oxigênio, relativamente fina, constituída principalmente de hematita (Fe2O3); seguida de uma camada intermediária, mais grossa, contendo magnetita (Fe3O4); e, por fim, uma camada mais próxima ao substrato, ainda mais espessa, pobre em oxigênio, basicamente formada de wüstite (composição que se aproxima de FeO).
Os principais agentes utilizados na decapagem química, essencial para remoção da carepa, são o ácido clorídrico e o ácido sulfúrico – por serem ácidos fortes –, eles têm alto poder de ataque às oxidações e carepas devido às suas altas taxas de dissociação. Fazendo um paralelo entre os componentes da carepa e os principais agentes utilizados para decapagem, a wüstite tem boa solubilidade nos dois agentes (ácido clorídrico e ácido sulfúrico), e quanto maior a concentração do agente, maior a sua solubilidade. Já a magnetita tem uma solubilidade menor, em relação à wüstite, para o ácido clorídrico – quanto maior a concentração do agente maior é sua solubilidade –; para o ácido sulfúrico, a concentração em si não tem grande interferências quanto a dissolução, mas a temperatura da solução sulfúrica, por sua vez, tem grande influência na solubilidade da magnetita. E, por fim, a hematita, que é de baixíssima dissolução nos dois agentes, é a grande responsável pela formação de borra nos banhos decapantes.
Comparativo entre os dois agentes decapantes:
a. Quanto à concentração, para os dois ácidos, é bem parecida, de 15% a 20% para o HCl, e entre 8% e 20% para o H2SO4.
b. Superfícies decapadas com ácido clorídrico tem a tendência a ficarem muito mais claras e brilhantes do que superfícies decapadas com ácido sulfúrico.
c. Obrigatoriamente, o decapante sulfúrico eventualmente necessita de aquecimento para uma boa performance, enquanto o decapante clorídrico na maioria das aplicações trabalha em temperatura ambiente.
d. Quanto ao consumo destes ácidos, na média, para dissolução de 60 g/m² de óxidos, consumimos de 150 a 157g de ácido clorídrico, em sua concentração comercial de aproximadamente 34%, e entre 75 e 88g para o ácido sulfúrico.
e. Quanto ao teor de ferro contaminante, por características dos agentes, o decapante clorídrico suporta até 200 g/L, enquanto o decapante sulfúrico, 130 g/L. Esse ferro contaminante é uma grande preocupação na etapa de decapagem, pois a contaminação limita a vida útil do banho decapante, gerando efluentes concentrados de tratamento trabalhoso. Visando retardar ao máximo essa contaminação por íons de ferro, proporcionando uma vida útil do banho decapante saudável, devem ser adicionados aos banhos, em doses relativamente baixas, agentes inibidores, que têm a principal função de inibir ao máximo o ataque ao substrato sem interferir na remoção de oxidações e carepas. Dependendo de sua formulação, os inibidores também agem na supressão de gases emanados pelo banho decapante. Em materiais a serem decapados com alto teor de carbono, a escolha de um agente inibidor de alta performance é imprescindível para evitar o efeito conhecido como overpickling, ou seja: a formação de fuligem sobre o substrato a ser fosfatizado.
Através de testes específicos, que serão relatados a seguir, podemos determinar a porcentagem de inibição da solução decapante ao substrato; essa inibição deve sempre tender a 100%, mas nunca atingir esta marca, pois, caso aconteça, o banho decapante estará tão inibido que não cumprirá a sua finalidade de remover os óxidos e carepas.
Consideram-se agentes inibidores de alta performance: produtos que tenham o poder de inibição entre 96% e 99%, conforme amostra de referência no gráfico abaixo. Assim, seguindo a orientação acima, teremos banhos decapantes com um ciclo de vida adequado à filosofia de sustentabilidade, ou seja, um ciclo de vida com o máximo de suas possibilidades, utilizado no máximo da performance, ótima qualidade de decapagem, não gerando efluentes e resíduos em demasia ou sem necessidade.
5. Banhos de camadas de conversão mais amigáveis ao meio ambiente
A substituição de fosfatos de zinco por nanocamadas (thin films) em processos de tratamento de superfícies é uma inovação que reflete o compromisso crescente com a sustentabilidade ambiental e econômica.
Tradicionalmente, o uso de fosfato de zinco, um composto empregado na preparação de superfícies metálicas para pintura e proteção contra corrosão, apresenta limitações ambientais e de saúde. O processo de fosfatização de zinco gera resíduos sólidos e líquidos que precisam de tratamento especial para evitar contaminação, além de consumir grandes quantidades de água e de energia. As nanocamadas, por sua vez, surgem como uma alternativa mais limpa e eficiente, com menor impacto ambiental e custo operacional.
Esses revestimentos utilizam uma camada ultrafina de materiais cerâmicos, que são aplicados nas superfícies metálicas para criar uma barreira altamente protetora contra a corrosão. Essa tecnologia não envolve metais pesados e reduz drasticamente a quantidade de resíduos e efluentes gerados durante o processo, diminuindo o impacto ambiental e as necessidades de tratamento de resíduos industriais.
Além disso, a aplicação de nanocamadas tende a exigir menor quantidade de energia, sendo mais rápida e, muitas vezes, compatível com uma ampla gama de materiais, como aço, alumínio e ligas metálicas, aumentando a versatilidade em diferentes indústrias, como a automotiva e a de eletrodomésticos.
6. Diminuição do uso de água em estágios de enxágue
O enxágue pós-tratamento é fundamental para remover o arraste de sais e aditivos dos banhos ativos do processo de conversão. Entretanto, a lavagem convencional, em estágio único, leva a um consumo elevado de água e a uma eficiência limitada de diluição. Nesse contexto, a implementação de métodos, como lavagem em cascata, permite otimizar a utilização da água, diminuindo a concentração de compostos residuais com menor volume de efluentes.
Quando se realiza o enxágue com arraste em uma solução de desengraxante a 200 g/L, a concentração na água de lavagem aumenta rapidamente nos primeiros ciclos de trabalho (considerando-se um limite de concentração no enxágue de 0,5 g/L), aproximando-se do valor assintótico do arraste. Nesse ponto, a quantidade de material que entra na lavagem torna-se equivalente ao que sai, estabelecendo um equilíbrio de fluxo. No entanto, alcançar essa estabilização em lavagem única pode tornar o processo ineficaz, já que a concentração se mantém em torno de 18 g/L após alguns ciclos, ultrapassando os limites adequados para a qualidade de lavagem.
A divisão do processo em uma lavagem tripla, com três compartimentos de 1.000 litros cada, dilui progressivamente a concentração de sais e aditivos no arraste. Em cada estágio, a concentração é reduzida de maneira significativa: a primeira etapa apresenta uma concentração de 0,2 g/L; a segunda, 0,0002 g/L; e a terceira, 0,0000002 g/L. Essa abordagem torna-se, portanto, 335 mil vezes mais eficiente em relação à lavagem simples, utilizando o mesmo volume total de água.
A cascata tripla, modelo de lavagem tripla em contrafluxo, aumenta ainda mais a eficiência ao introduzir água limpa na última etapa e utilizá-la de forma contínua e contrária ao fluxo das peças. Essa técnica leva a uma concentração de sais, na última etapa, de apenas 0,174 g/L. A adição de um sistema de spray na terceira etapa reduz ainda mais essa concentração, para 0,0498 g/L, demonstrando que o uso de múltiplos estágios e a introdução de fluxo controlado aumentam significativamente a eficiência do enxágue com o mínimo de água.
7. Comparação da eficiência no uso da água
Um comparativo entre os métodos de lavagem única, cascata dupla, tripla e tripla com spray evidencia a eficiência da redução de concentração de sais no efluente, com destaque para a economia de água:
- Lavagem única: concentração de 18,0 g/L
- Cascata dupla: concentração de 1,76 g/L
- Cascata tripla: concentração de 0,174 g/L
- Cascata tripla com spray: concentração de 0,0498 g/L
Esse escalonamento indica que a utilização de lavagens em múltiplos estágios, associada a tecnologias de enxágue de recuperação, reduz drasticamente o volume de efluente e a carga de sais e orgânicos na saída. Além disso, alcança-se uma retenção mais eficaz dos materiais, reduzindo a frequência de reposições e o custo com anodos e compostos adicionais.
A implementação de técnicas de lavagem tripla e cascata tripla, especialmente com enxágue de recuperação, revela-se uma prática sustentável e econômica para o setor de galvanoplastia. Com essas abordagens, reduz-se drasticamente o consumo de água e a carga de efluentes, promovendo a eficiência do processo e contribuindo para uma gestão de recursos mais consciente e responsável.
8. Considerações finais
A adoção de práticas sustentáveis em processos industriais, especialmente nos de camadas de conversão e pré-pintura e conformação frio, é fundamental para atender às crescentes demandas por eficiência ambiental e responsabilidade socioeconômica. Ao longo deste artigo, foram exploradas abordagens inovadoras que demonstram como as indústrias podem reduzir impactos ambientais por meio da otimização de processos e da substituição de agentes poluentes.
Desde a separação dos efluentes até o uso de nanocamadas no lugar de fosfatos de zinco, além de técnicas mais eficientes de lavagem, cada etapa reflete um avanço rumo a um modelo de produção mais limpo e consciente.
Nesse contexto, a busca por sustentabilidade vai além de um objetivo ambiental; ela proporciona vantagens competitivas, como a redução de custos operacionais e o aprimoramento de processos, promovendo um ciclo de economia circular que beneficia tanto a indústria quanto o meio ambiente. Ao minimizar o uso de recursos naturais e o descarte de resíduos, tais práticas revelam-se essenciais para a perpetuação de um setor industrial que valoriza o desenvolvimento sustentável.
Assim, é possível concluir que a incorporação de práticas sustentáveis em processos complexos de conversão e tratamento de superfícies é não apenas viável, mas necessária. Esse compromisso com a sustentabilidade garante à indústria a capacidade de evoluir sem comprometer as futuras gerações, demonstrando que inovação e responsabilidade ambiental podem coexistir e reforçarem-se mutuamente em um modelo de produção alinhado aos desafios do século XXI.