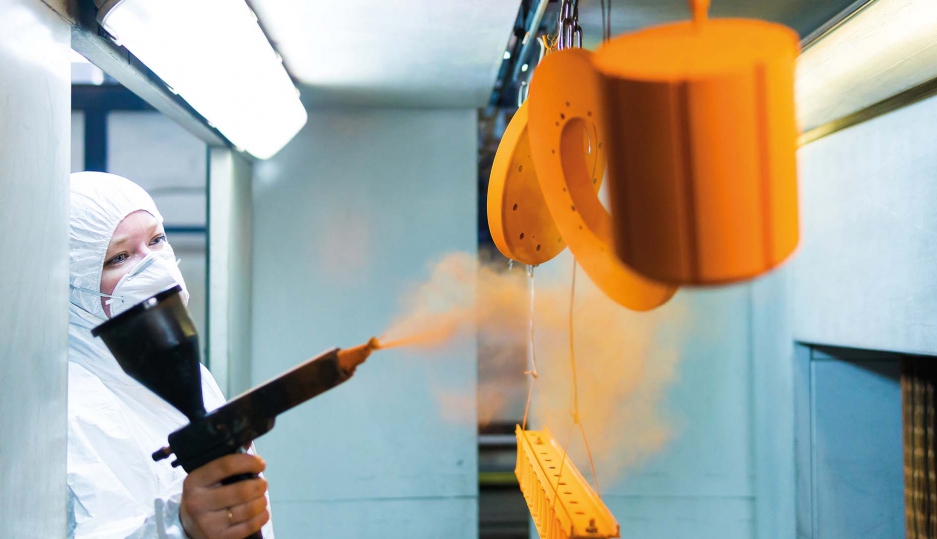
Do início da tecnologia até os dias de hoje, um guia sobre a pintura industrial mais utilizada no mercado
Consultor Sênior, Eritram Coatings
Quando pensamos em pintura industrial de alto desempenho e de uso geral, logo vêm às nossas mentes a tinta industrial a pó. Essa tecnologia, conhecida desde os anos de 1960, teve um impulso vertiginoso na década de 70 em diante e hoje é considerada uma das líderes em utilização no segmento. Estima-se um consumo superior a 40 mil toneladas por ano no Brasil.
Os primeiros trabalhos com revestimento aplicado a pó, citam algumas literaturas sobre o tema, foram feitos por Pieter de Lange, pesquisador da DuPont nos idos de 1961, quando desenvolveu material e pistolas para aplicação de resinas, endurecedores e pigmentos na forma de pó.
No entanto, anteriormente, em 1953, o Dr. Erwin Gemmer, cientista alemão, já havia patenteado um processo de revestimento em câmara fluidizada com tinta em pó.
Esses materiais, como regra para todas as aplicações de pintura industrial, requerem um substrato convenientemente preparado para receber o revestimento orgânico de proteção contra a deterioração do tempo e que atente aos requisitos estéticos do objeto a ser pintado.
O sistema de pintura em pó mais utilizado é o por pulverização eletrostática de aplicação, pelo processo Corona, e o pó, uma vez aderido à peça vai ao forno, onde funde-se, espalha e retícula, formando um filme duro, aderente e de brilho, cor e aparência desejados. Trata-se de um sistema relativamente simples e confiável de pintura, desde que existam as condições necessárias para a operação.
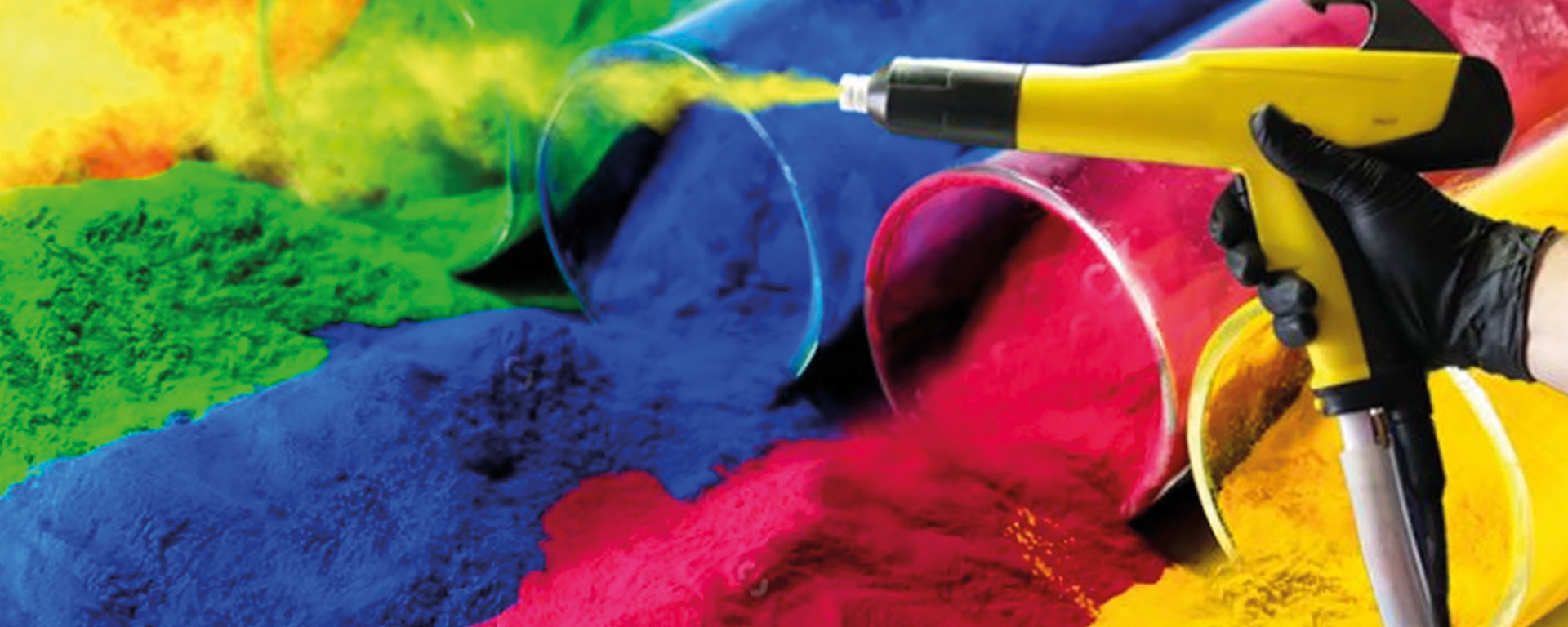
Por ser um produto em pó com baixíssimo teor de voláteis, o seu rendimento teórico é quase que total, por volta de 95%. No entanto, nas condições de operação no dia-a-dia, esse rendimento poderá ser menor dependendo do processo utilizado. Um cuidado que se deve tomar, e que muitas vezes passa despercebido, é com relação à quantidade, algumas vezes apreciável, de resíduos de tinta gerados na operação – que, na maioria dos casos, irá direto para o descarte, ocasionando custos adicionais importantes.
Requisitos
Os requisitos básicos para uma boa pintura começam na obtenção de um substrato convenientemente preparado, com ausência de corrosão, oleosidade, poeira e sujeiras, preferivelmente, com um tratamento de proteção à corrosão, tais como a fosfatização.
Muitas peças pintadas com tinta em pó recebem somente limpeza superficial ou um tratamento por jateamento de granalha que, em muitos casos, atende às solicitações exigidas para um determinado objeto.
Os equipamentos de pintura compõem-se de uma cabina de aplicação específica, pistolas eletrostáticas, ventilação adequada, exaustor para captação do pó não aderido à peça, sistema de filtros de ar, ciclones para recuperação da tinta e posterior reaproveitamento, etc.
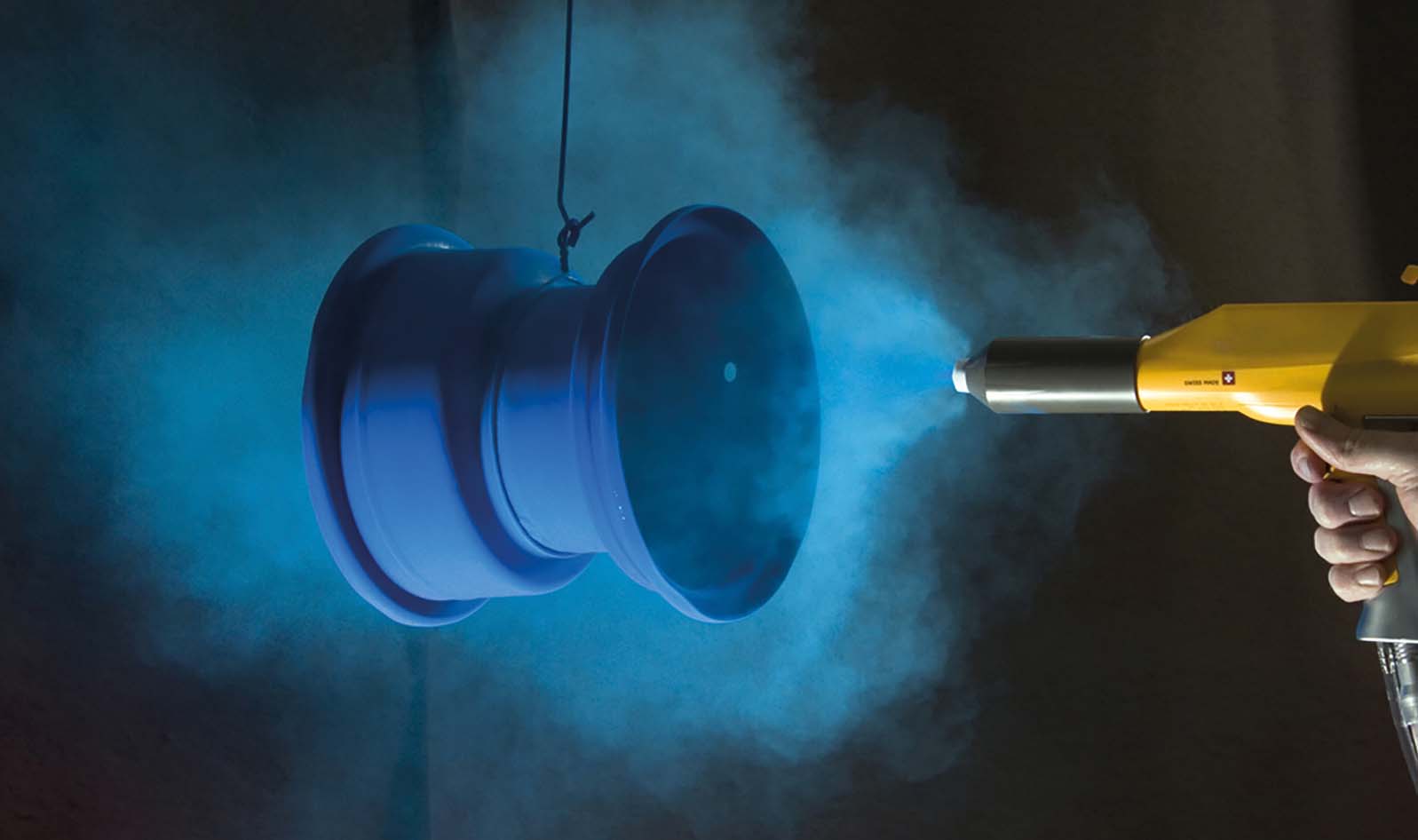
Se a cabine de pintura não possuir um bom controle de temperatura e umidade poderá incorrer em variações na aplicação de tinta a cada momento. Uma tinta aplicada a 200º Celsius, e com umidade relativa de 90%, se comporta radicalmente diferente dela mesma aplicada a 15º Celsius, com umidade relativa de 30%. Portanto, seguir corretamente as especificações do equipamento e do fabricante de tinta é fundamental para um funcionamento contínuo, evitando ajustes a cada momento nas vazões de pistolas e demais parâmetros da operação.
Posteriormente, será necessário ter uma estufa programada para atingir até 220º Celsius, com temperatura do ar circulante, a fim de obter a cura especificada.
A polimerização eficiente da tinta será fundamental para obter as melhores propriedades químicas e mecânicas do filme aplicado. Sendo assim, seguir as recomendações de cura feitas pelo fabricante de tinta será de fundamental importância.
O boletim técnico do produto emitido pelo fabricante informará o tempo e temperatura de metal na qual a peça deverá ser submetida. No entanto, o tempo que a mesma deverá permanecer na estufa depende da espessura, massa e disposição da peça, além das características e tipo de forno utilizado. Como exemplo, se a solicitação de cura para determinado revestimento é de 10 minutos a 170º C, como temperatura de metal (MT), a peça poderá permanecer até cerca de uma hora dentro da estufa para atingir o tempo e temperatura especificados. Portanto, é fundamental medir com termógrafos confiáveis o patamar de cura à qual a peça foi exposta.
A grande maioria das tintas em pó tem a característica de mascarar diferenças significativas de cura, não sendo possível, em muitos casos, a visualização através da cor e brilho ou aparência final. O controle de qualidade da pintura, além do monitoramento dos paramentos de processo dentro das especificações, será de muita valia na liberação do material em sua melhor forma e propriedades.
Solucionando
As gancheiras onde as peças são penduradas são uma das grandes causadoras de problemas de aplicação. Assim, quando mantidas e operadas corretamente contribuirão para obter uma maior eficiência de pintura no processo. Espaçamentos e posicionamentos corretos das peças com boa acessibilidade de pintura e um bom contato delas com as presilhas das gancheiras são fundamentais para obter uma pintura na condição desejada.
Do ponto de vista de segurança, todos os objetos eletricamente condutivos na área de aplicação da tinta, exceto os que são conectados em alta voltagem, deverão estar aterrados com resistividade inferior a um megaohm. Uma correta fixação e aterramento da peça poderá levar a melhor utilização de tinta, aumentando em até 15% a eficiência de transferência, reduzindo, assim, perdas de material e refugos.
Com essas medidas, o sistema de pintura terá maior utilização, com aumento de velocidade da linha, reduzindo tinta e insumos utilizados, menos material para a reciclagem ou descarte, menor nível de defeitos e rejeitos, aumentando, assim, a eficiência de transferência no primeiro passe.
A correta distribuição de tinta sobre toda a peça com a obtenção da espessura do filme especificada é também um item fundamental para evitar rejeitos e perda de dinheiro, além de negócios. Chamamos a atenção para proceder à medição de espessura com aparelho de boa qualidade, aferido e com a peça fria, a fim de se ter números confiáveis.
Como exemplo, se o requisito de filme seco é da ordem de 75 a 100 micra e estiver trabalhando na linha na faixa de 100 a 125 micra o custo da pintura em relação ao item tinta, aumentará em cerca de 30%, não trazendo na maioria dos casos nenhum benefício, ou até alguma deficiência em aparência, nas propriedades mecânicas, como impacto e aderência, além de dificultar o ajuste do componente a uma outra parte do conjunto, quando houver.
A distribuição homogênea da tinta em pó sobre a peça é um dos desafios a ser superado nesta tecnologia. Áreas de difícil acesso ou de oclusão provocam as chamadas caixas de Faraday onde o pó não alcança toda a superfície e também não adere corretamente ao substrato.
A voltagem flui pelas áreas de menor resistência e o pó tende a fluir através das correntes de voltagem e, preferivelmente, nas áreas planas. Para reduzir os efeitos da má distribuição de tinta, além do perfeito aterramento já discutido acima, o ajuste de voltagem e amperagem, fluxo de tinta pulverizada, distância adequada entre peça e pulverizador, entre outras, são de fundamental importância para o processo.
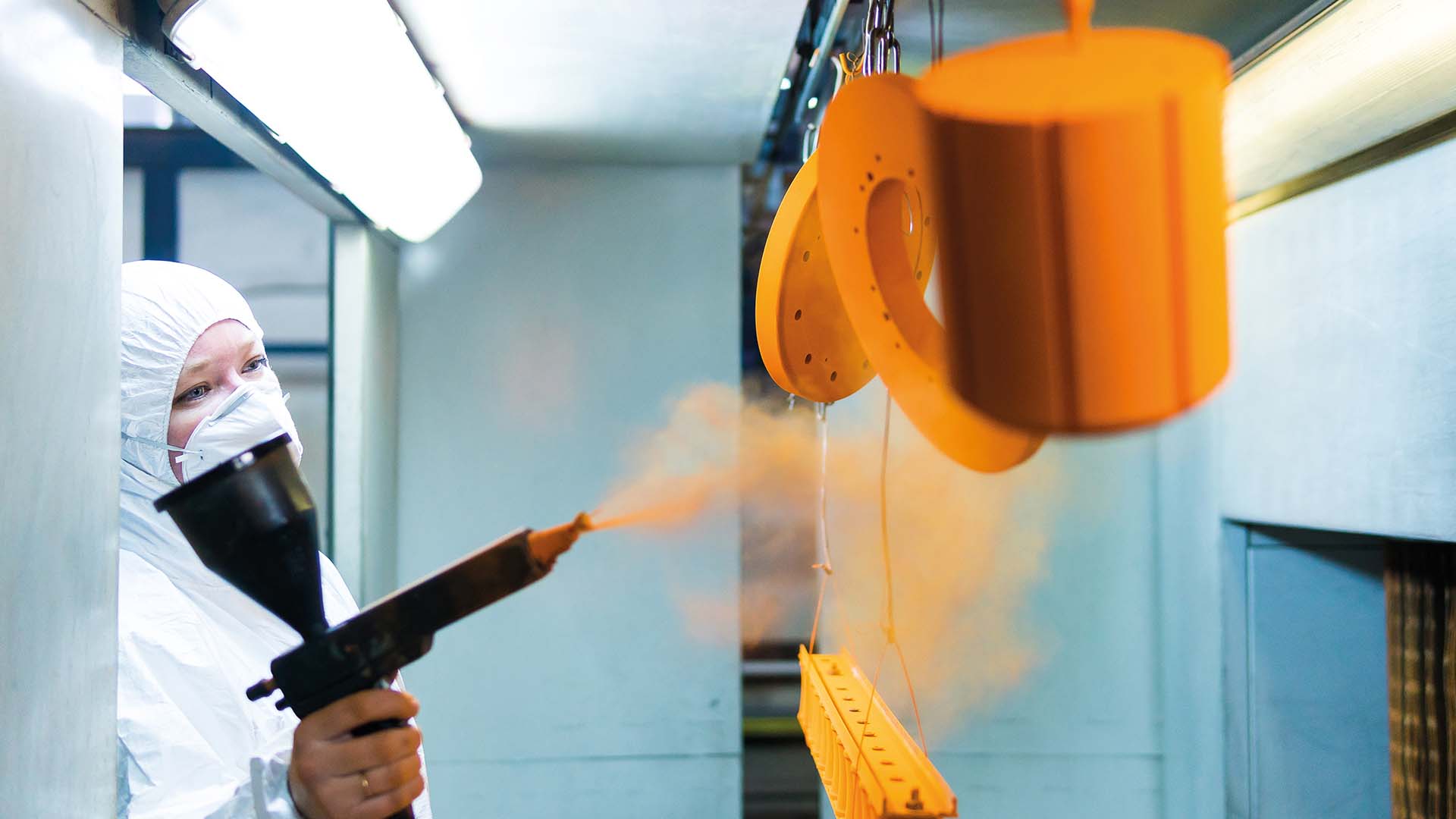
Uma das coisas mais importantes
Um dos pontos vitais no sucesso da aplicação deste tipo de tinta é ter pintores corretamente treinados, conhecedores das variáveis envolvidas no processo e seus efeitos negativos à pintura. Devem estar usando os EPIs (Equipamentos de Proteção Individual) exigidos para esse tipo de operação, além, é claro, de equipamentos, como cabina, pistolas e forno em perfeito estado e corretamente mantidos e controlados.
O investimento que se faz para treinar um profissional é oneroso e demorado, por isso a importância de remunerá-los corretamente e treiná-los constantemente, além de motivá-los na busca permanente da melhor qualidade e eficiência na operação como reduções de tempo e desperdícios.
Sendo este um assunto vasto, que abrange muitas outras etapas fundamentais da tecnologia, e que está além do escopo deste artigo, recomendamos aos especialistas e usuários revisitar todas as fases de vossos processos com maior profundidade, a fim de determinar ganhos técnicos e econômicos através da correta utilização desta fantástica tecnologia.
Acesse o conteúdo original Publicado na revista Tratamento de Superfície, edição 220, página 18-20