Este resumo pode ser alarmante ou exagerado, mas aconselho que levem em consideração estas reflexões que minimizam riscos e perigos presentes diariamente em nossa indústria
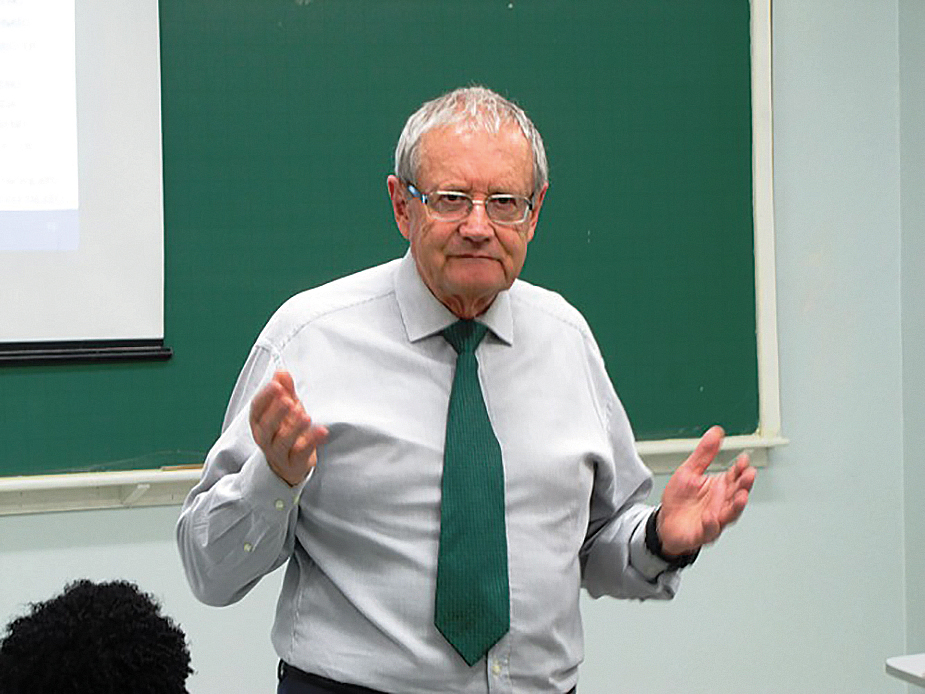
Hugo A. Haas
Dr. em Química UBA, membro e professor da Associação Tecnológica Ibero-Americana de Pinturas, Adesivos e Tintas na Argentina (ATIPAT)
Estas reflexões não pretendem ser um manual de segurança industrial, mas de forma resumida, busca chamar atenção quanto a algumas causas pelas quais o risco de incêndio está sempre presente e é uma preocupação permanente para todos que trabalham nas fábricas de tintas.
As fábricas de tintas, adesivos, empresas de pintura e outras relacionadas utilizam grande variedade de materiais, usualmente perigosos, como solventes, resinas, vernizes, e outras matérias-primas, sendo, a maioria, combustíveis. Há também indústrias como as de tinta pó (não cal), que, apesar de não utilizar solventes na mesma proporção, também correm riscos de incêndios e explosões.
1. Imprudências
Muitas vezes são negligenciados os riscos de incêndios ativos nas imediações da unidade fabril realizam ou dos depósitos, e se realiza atividades no interior da fábrica, como marteladas, manipulação de alavancas, operações de soldagem etc.
Fumar é comum e muito perigoso. Soldar equipamentos também é bastante comum.
Há casos de comemorações, em algumas circunstâncias, em que se faz churrasco, manipulando fogo, por exemplo, sem tomar a precaução de que seja feito em local suficientemente longe e isolado de possíveis faíscas.
2. Instalacões
Apesar de muitas vezes as instalações serem projetadas e construídas por profissionais, há erros que podem ser a causa de incêndios e explosões. Sem dizer que, por vezes, as instalações são construídas por profissionais não qualificados.
Instalações elétricas merecem cuidado especial; deve-se evitar chaves e conectores que liberem faíscas quando acionadas ou desconectadas, fato inevitável dado a FEM de ruptura. Portanto, o ideal é instalar caixas antiexplosivas, com botões de baixa voltagem (usualmente de 12 ou 24 volts) localizadas o mais alto possível ou a uma respeitável distância do equipamento que comandam.
Os contatores térmicos correspondentes deverão estar localizados no quadro geral, que preferencialmente devem estar fora ou afastados do recinto fabril. Os motores devem ser antiexplosivos e 100% blindados, as conexões feitas com cabos e terminais adequados e fixados com parafusos. O quadro elétrico geral (preferencialmente fora do recinto fabril) deverá indicar a voltagem de cada fase e ter um amperímetro que indique o consumo. Cada equipamento deve estar conectado a um cabo terra efetivo e não somente ao cabo terra da companhia elétrica.
Outro aspecto das instalações que merece destaque é o sistema de ventilação. Não podemos esquecer que os vapores dos solventes são mais pesados que o ar, por conseguinte tendem a se concentrar perto do piso. Assim os exaustores ou ventiladores devem considerar esta condição já que, colocando exaustores na parte superior do edifício, só expelirão ar limpo. Instalações bem planejadas têm ventiladores e exaustores no nível do piso, provocando um direcionamento dos vapores de solventes para o exterior. Por isso, canaletas, nichos das balanças e qualquer outra cavidade devem ser evitadas, já que nos mesmos se concentrarão os vapores de solventes e, no momento em que exista um estímulo, podem incendiar-se ou explodir. Isso nos obriga a considerar as misturas explosivas formadas entre os vapores de solventes e o ar, de variada composição, o que aumenta muito o risco.
Após uma análise das possíveis causas desses fatos, resumimos as causas mais comuns:
- Imprudências;
- Instalações;
- Matérias-primas, resinas, solventes, nitrocelulose, sacos plásticos e outros materiais de embalagem;
- Eletricidade estática, Reações exotérmicas;
- Lixo;
- Planta de resinas e vernizes.
3. As matérias-primas
Nessas indústrias trabalha-se com uma grande variedade de matérias-primas algumas não combustíveis e outra parte considerável altamente combustível e perigosa.
Algumas instalações descrevem essa situação no código do produto. Por exemplo, o código poderia estar precedido da letra “P”, o que indicaria que esse material é “Perigoso” ou outra indicação como referente à toxicidade, etc.
As resinas habitualmente são dissolvidas em solventes inflamáveis, por isso devemos tratar como se fossem solventes puros. Há matérias-primas como a nitrocelulose, que são altamente perigosas, caso especialmente crítico. O material é entregue molhado em álcool (etanol, isopropanol, butanol, plastificante, etc.) para que a nitrocelulose seja manuseada com bastante segurança. Porém, se estiver seca, o risco de explosão é certo. Portanto, os tambores em que são entregues o material devem ser girados de cabeça para baixo e cabeça para cima, de modo que o material esteja sempre molhado. De preferência, convém usar um tambor cheio para não deixar restos que possam secar. A nitrocelulose também se decompõe facilmente quando chega próxima dos 120 ºC. Por isso, em operações de dissolução em dispersores de alta velocidade, é usual que a borda do disco chegue a essa temperatura, o que provoca inicialmente vapores avermelhados (de óxidos de nitrogênio) por decomposição da nitro e provável “flash” e incêndio. A dissolução da nitro poderia ser feita também com um agitador lento se molharmos previamente com os não solventes, e agregando rapidamente os solventes verdadeiros, com isso a solução seria feita imediatamente.
Outra matéria-prima crítica são os peróxidos. Alguns são usados para os vedantes automotivos e outros como catalizadores na fabricação de resinas acrílicas. Devem ser manipulados cuidadosamente, e mantidos em depósito isolado.
Na manipulação de solventes devem ser tomadas as precauções descritas mais detalhadamente ao tratar do problema da eletricidade estática, mas, em geral, deve se considerar que a agitação excessiva não só irá aquecer as misturas, mas também causar perdas pela evaporação.
4. A eletricidade estática. As reações exotérmicas:
Muitos incêndios em fábricas de tintas ocorrem devido à manipulação equivocada, desconhecimento da eletricidade estática, falta de controle das reações exotérmicas, pós-orgânicos e metais finamente divididos.
É certo que nem todos os operários estejam conscientes e nem creem nos perigos da estática. É imprescindível instruí-los quanto a esse fenômeno, com alguns exemplos práticos, como levantar papeizinhos com um pente que se esfregou antes ou fazer menção aos choques que percebemos muitas vezes ao descer de um veículo, etc.
A fricção na operação de transporte, durante o processo, na transferência, entre outras operações igualmente críticas, faz com que se forme um potencial eletrostático considerável, que, ao descarregar, pode produzir carga provocando, inevitavelmente, um incêndio ou uma explosão. Por isso, temos quatro princípios básicos que são:
- Aterramento eficaz;
- Continuidade elétrica;
- Atmosfera inerte;
- Recipientes com lixo.
Cada máquina da produção deve estar aterrada a um sistema central conectado a uma ponteira ou uma rede de ponteiras que garantam um aterramento eficaz. Não é conveniente basear-se somente no cabo terra fornecido pela companhia de eletricidade.
É comum que as fábricas utilizem, além dos tanques de diluição, baldes ou potes de tamanhos variáveis, transportados sobre rodas ou ponte rolante ou, ainda, empilhadeiras. Cada balde deve ter um cabo ou cinta condutora que arraste sobre o piso.
Nesses recipientes (que jamais podem ser de plástico) e nos tanques de diluição se misturam resinas, concentrados de pigmentos, aditivos, solventes, etc., para completar a formulação ou fazer correções. Do balde ou tanque ao recipiente que contém a mistura, deve haver continuidade elétrica. Isso se consegue com um cabo terra com duas presilhas (jacaré), prendendo cada uma a cada recipiente ou apoiando bem o tambor, ou balde metálico, também sobre a borda de um balde (recipiente), de modo que estejam ligados eletricamente.
De qualquer forma, é sempre uma medida de segurança muito importante não ter dentro da fábrica recipientes com resíduos de tintas, solventes, etc., tecidos e papéis que possam ter combustão espontânea. É comum que os incêndios em fábricas de tintas, que não têm explicação clara, tenham se iniciado nas lixeiras. Elas devem estar sempre vazias e limpas no final do dia, e nunca permanecer dentro da fábrica quando se trabalha. Devem ser deixadas fora do local da fábrica.
EM NENHUMA CIRCUNSTÂNCIA FAZER MISTURAS USANDO UM BALDE OU TAMBOR PLÁSTICO.
Essa é uma prática muito usada, mas muitas vezes causa incêndios por uma faísca estática.
A descarga dos caminhões tanques que trazem solventes também deve ser feita com cuidado. Durante o transporte, o líquido no tanque produz uma considerável carga estática. Deve-se descarregar antes da abertura das válvulas que conectam o caminhão tanque com o reservatório da fábrica.
O aterramento deve ser conectado ao caminhão tanque, a uma mangueira de descarga, geralmente coberta por uma espiral de metal e medida com um “tester” até que não se detecte mais carga estática. Isso pode demorar bastante quando se descarrega solventes alifáticos e aromáticos, e quase imediatamente quando se descarrega solventes oxigenados.
Muitas matérias-primas são entregues em sacos plásticos de polietileno, geralmente carregados eletrostaticamente, por isso se deve cuidar desse detalhe, pois existem polietilenos que não apresentam esse problema.
RISCOS DE EXPLOSÃO E INCÊNDIO NA FABRICACÃO DE TINTA EM PÓ
Descarga proveniente de energia em mJ
Faísca | 0,5 |
Faísca de uma ferramenta | 2 |
Faísca proveniente de um tambor de 200 lts | 40 |
Faísca proveniente de um ser humano (roupas de nylon...) | 10-30 |
Faísca proveniente de grandes objetos metálicos | 50-100 |
Descargas de fricção de elementos não condutores (grandes sacos plásticos, superfícies empoeiradas, tubos plásticos etc.) | 3-5 |
É comum pensar que como as tintas em pó não contêm solventes, não se corre risco de incêndio ou explosão durante sua fabricação, manuseio ou uso, mas todas as matérias-primas, caixas de papelão, sacos plásticos etc., exceto os pigmentos e cargas inorgânicas, são combustíveis. Os pigmentos metálicos (especialmente alumínio e zinco) são especialmente perigosos (em determinadas condições, temperatura ambiente e umidade). Felizmente, as resinas e pigmentos orgânicos têm inflamabilidade muito baixa, por isso é improvável a autoignição. Porém, em caso de incêndio, esses materiais se queimarão sem alternativa.
De toda forma, é sempre uma medida de segurança importante não ter dentro da fábrica recipientes com resíduos de tintas, solventes etc., panos e papéis que podem ter combustão espontânea, pois, conforme já comentamos, incêndios em fábricas de tinta podem começar nos recipientes de lixo. Eles devem estar sempre vazios e limpos ao final do dia.
Outra causa muito comum de incêndios são as descargas eletrostáticas. Para o caso específico da fabricação de tinta em pó, devemos lembrar que se manuseia muita coisa em sacos plásticos de polietileno, que estão carregados eletrostaticamente e podem produzir faíscas, às vezes, de intensidade regular, podendo causar incêndios ou explosões. A eletricidade estática gerada pelas máquinas - em movimento ou nos dutos de transporte do pó em geral - é descarregada pelos aterramentos (cabo terra) que normalmente têm nas instalações. Em casos de dutos mais ou menos largos, deve-se introduzir neles um cabo terra descascado.
Porém, essas condições são diferentes quando se pensa nos riscos de explosão, especialmente nos casos de produção que envolvam pigmentos metálicos. Portanto, na produção desses produtos deve-se considerar os riscos do processo.
As explosões que acontecem em instalações onde contém pó orgânico finamente divididos são bastante comuns, inclusive em instalações nas quais não se pensa nesse risco, como nos silos de armazenagem.
A matéria orgânica dividida em partículas muito pequenas, em contato íntimo com o ar e em certas condições de umidade e temperatura, e sob a influência, ou não, de um desencadeante, como uma faísca ou outra fonte de ignição, se oxidam instantaneamente produzindo uma explosão.
As tintas em pó, assim como os pós metálicos finamente divididos, quando uma certa quantidade é dispersada na atmosfera são potencialmente explosivos. Se simultaneamente existe uma fonte energética suficientemente poderosa, poderá produzir a ignição, que geralmente toma a forma de explosão.
A quantidade de energia necessária para inflamar uma nuvem de pó de alumínio depende, em primeiro lugar, da distribuição do tamanho e forma das partículas, e, em menor grau, do tratamento superficial que tenha esse pó. Outros fatores como a temperatura ambiente e umidade, podem também desempenhar um papel na ignição da nuvem.
A facilidade de inflamação é definida por um parâmetro chamado: Energia Mínima de Ignição - MIE: (Minimum Ignition Energy). Os níveis de MIE vão desde 1 mJ até 50 mJ. Os materiais com forma laminar têm o mais baixo nível de energia.
Embora uma explosão ou a combustão de uma nuvem de pó seja pouco comum, não podemos deixar de lado ou ignorar o risco. A ignição de uma nuvem de pó contendo metais finamente divididos, pode certamente ocorrer pela ação de uma faísca produzida pela eletrostática formada nas roupas dos operadores (camisas, regatas, camisetas de poliéster ou nylon, pulôveres de poliéster, etc.). O mesmo poderia acontecer por uma faísca produzida pela junta de um misturador ou um motor superaquecido ou não blindado.
Caso aconteça a explosão de uma nuvem de pó de alumínio, a violência pode ser muito grande. Esta medida da força da explosão é mensurada através do Parâmetro Kst. Isso depende do valor máximo do aumento da pressão em uma explosão em um ambiente não arejado.
Os valores para o pó de alumínio puro estão entre 300 e 1000 bar.m/s.
A gravidade da explosão será significativa mesmo para quantidades da ordem de 1 kg, e como é muito difícil de se proteger contra essas explosões, deve-se então tomar as medidas de precaução adequadas.
As nuvens de tinta em pó são por si mesmas potencialmente explosivas. A energia mínima de ignição depende, sobretudo, do tamanho das partículas e, em menor escala, da composição.
Para partículas finas (3 a 4 µm) foi detectado um valor próximo a 1-3 MJ. Porém, o mais comum é ter partículas mais grossas de poeira. Assim, em geral os valores para MIE são fixados na ordem de 10 a 30 MJ.
A gravidade das explosões de tinta em pó tem uma gama de valores que vão de 100 a 200 bar.m/s. O valor de 200 se refere a materiais muito finos.
Uma explosão desse tipo, seria muito menos violenta do que uma de alumínio puro, mas poderia causar danos consideráveis.
Ao misturar pó de alumínio com tinta em pó, aumenta-se o Kst em aproximadamente 10%, enquanto a proporção de alumínio não supere 5-6%, somente quando a proporção de alumínio chegar perto de 25%, o valor do Kst é similar ao do alumínio puro.
A energia mínima de ignição (MIE) diminui apenas quando se usa mais de 10% de materiais em forma laminar muito fina. Deve-se considerar, também, que se o alumínio é separado poderá alterar os dados para um Kst mais elevado e uma MIE mais baixa.
Os riscos diminuem muito quando se trabalha em atmosfera inerte de nitrogênio, prática bastante aconselhável.
5. O Lixo
É muito comum que os restos de vários tipos de lixo, panos que se limparam sobras de resina ou tinta, etc., sejam colocados em um tambor ou outro recipiente qualquer.
A matéria orgânica sofre oxidação, que é exotérmica, e como nesses recipientes não há muita troca com o exterior, podem chegar a inflamar e causar incêndios. Muitos incêndios são causados por esse descuido. Um recipiente com resíduos nunca deve ser deixado a noite toda no interior da fábrica. Deve ficar em lugar especial, do lado de fora. É muito importante enfatizar que os recipientes com lixo não fiquem na área fabril à noite, e sempre estejam limpos sem conter resíduos de dias anteriores.
6. Planta de resina e vernizes
Atualmente, as plantas de resinas têm equipamentos e instalações muito bem preparadas, visando a segurança. Entretanto, deve-se tomar precauções para evitar desastres.
Durante a síntese de muitas resinas, ocorrem reações exotérmicas que devem diminuir durante o processo.
Tomando como exemplo a síntese de resinas alquídicas na primeira parte da esterificação ocorre uma forte reação exotérmica com abundante produção de espuma. O reator deve estar equipado com controle de calefação, quebra de espuma, etc. e também deve estar sempre conectado através de um disco de ruptura, com um reservatório que, eventualmente, transborde o reator se o processo não estiver contido (“catch-tank”).
O caso mais perigoso é o da polimerização de monômeros acrílicos que se realiza com a intervenção de certos peróxidos especiais.
O processo é realizado carregando o solvente e se esquentando até a ebulição. É importante que a temperatura em que o solvente ferve, coincida ou seja pouco maior que o da decomposição do peróxido. Uma vez que o solvente ferve, carrega o monômero, ou a mistura deles, dosificando-o conjuntamente com uma solução do peróxido. Precisamente, o perigo está no peróxido que não se dissolver simultaneamente com a polimerização dos monômeros, que ao se acumular, podem se decompor rapidamente e, consequentemente, causar uma inevitável explosão.
Amigos, este resumo pode ser alarmante ou exagerado, mas aconselho que levem em consideração estas reflexões para minimizar riscos e perigos que estão presentes diariamente em nossas indústrias.
Acesse o conteúdo original publicado na revista Tratamento de Superfície, edição 218, página 43-47