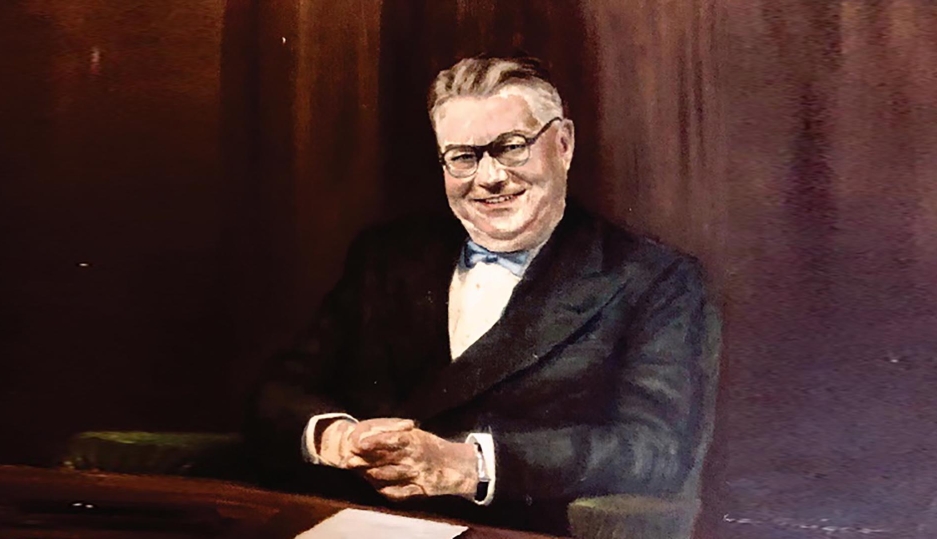
Figura 1 – Engenheiro Químico Richard Ostrander Hull (12/04/1905 – 29/11/1957), Reprodução fotográfica de pintura em tela, gentilmente cedida ao autor por seu filho Harry F. Hull.
Saiba como surgiu a ferramenta que transformou para sempre o controle da qualidade nos banhos da indústria galvanotécnica
Pedro de Araújo é Consultor Galvanotécnico e Ambiental, Owner da PA8 Consultoria e Mentoria Galvanotécnica e Ambiental*
Introdução
A Célula de Hull está entre as melhores ferramentas analíticas para o controle da qualidade dos ‘banhos’ usados na eletrodeposição de metais. Foi criada nos idos da década de 1930, pelo americano Engenheiro Químico Richard Ostrander Hull (Figura 1), tendo a primeira patente requisitada, pela Dupont, em 1935 e concedida sob n° US 2.149.344 em 7/03/1939 (Figura 2); a segunda patente foi concedida em 1957, em seu nome, e a terceira patente em nome de seu filho Richard O. Hull Jr, em 1964.
Com este artigo, rende-se homenagem ao Engenheiro Químico R.O. Hull, reverenciando sua memória nos últimos 88 anos da prática galvanotécnica, por sua criatividade, genialidade e grande contribuição para a eletroquímica.
Atualmente, há mais de uma dezena de patentes para células eletroquímicas derivadas da primeira patente de R.O. Hull, algumas concedidas neste século 21.
A tela reproduzida na Figura 1 foi um presente dado por funcionários da R. O. Hull & Company - Cleveland, Ohio, USA, aos seus filhos Richard O. Hull Jr e Harry F. Hull, atual guardião da obra.
Harry F. Hull fez o seguinte relato a este autor: “Richard O. Hull foi graduado em Engenharia Química, pela Universidade de Colorado e iniciou Mestrado na Universidade Georgetown em Washington, D.C., sem concluir a pós-graduação. O primeiro emprego dele foi na RCA (eletrônica), que estava desenvolvendo discos e sistemas para reproduzir som. O trabalho do Hull foi desenvolver eletrodeposição de níquel para fazer matriz de estampagem dos discos de baquelite. Com a depressão nos Estados Unidos da América, na década 1930, a RCA fechou a unidade de pesquisa. Durante quase dois anos, sem emprego, a família foi morar com os sogros na Carolina do Sul. Com o fim da depressão, Hull conseguiu emprego na E.I. Dupont de Nemours & Co., no Laboratório Grasselli em Cleveland, Ohio. Lá, ele pesquisou aditivos para banhos de galvanoplastia, principalmente zinco e cádmio. Por volta de 1935, ele inventou a Célula de Hull, que resultou na sua patente em 1939, pertencente à DuPont. Em 1944, saiu da DuPont para abrir a sua empresa, a R.O. Hull & Company Inc., em Cleveland, Ohio, vendendo aditivos para zinco, cádmio, cobre e cromo, e, obviamente, a Célula de Hull. Durante muitos anos ele pagou royalties para DuPont sobre as vendas da sua invenção, Célula de Hull, até a expiração da patente, em 1956. Ele continuou com a empresa até 1957 quando faleceu, repentinamente, com a idade de 52 anos. Os primeiros produtos da Rohco eram abrilhantadores para zinco, cádmio, cobre e um molhador para cromo para diminuir ‘spray’. Quando eu tinha 5 anos (1945), a família inteira se reunia para cortar os cantos pontiagudos de cátodos para Célula de Hull. A Rohco se estabeleceu no Brasil em 1972; nos EUA foi subsidiária da Lubrizol Co., entre 1973 e 1978. Eu vim para o Brasil em 1976 e logo assumi a filial brasileira, em 1977. A Rohco Inc., de Cleveland, Ohio, foi adquirida, em 1982, pela McGean Chemical, formando a McGean-Rohco Inc., e a filial brasileira permaneceu em operação usando o nome original até 1991, quando foi absorvida por Roshaw Química”.
De acordo com a história da McGean, em sua página na internet, com a formação da McGean-Rohco, a empresa tornou-se líder em galvanoplastia e tecnologia de acabamento de metal e, em 1991, adquiriu o negócio de química de placas de circuitos impressos da E.I. DuPont; em 2001, vendeu os negócios mundiais de galvanoplastia, acabamento de metais e produtos químicos eletrônicos para a Atotech (EUA/Alemanha). Atualmente, a McGean é uma indústria fabricante mundial de especialidades químicas.
Figura 2 – Primeira patente da Célula de Hull, 1939, página 1.
Como funciona a Célula de Hull
A Célula de Hull é um tanque de eletrodeposição, de formato específico, onde o cátodo está propositalmente inclinado em relação ao ânodo, em ângulo aproximado de 40°. A corrente necessária para a eletrólise é fornecida por um retificador e pode ser contínua, de onda convencional, pulsante, ou de pulso reverso, dependendo do eletrólito e processo em estudo. Na Célula de Hull, a densidade de corrente varia ao longo do cátodo e é possível, através da equação de Hull, encontrar em determinada posição do cátodo a corrente ideal para obter melhor revestimento metálico.
O uso da Célula de Hull é normatizado desde 1962, conforme DIN 50957-1:2016-02, Teste de eletrólitos usados para revestimentos metálicos eletrodepositados - Teste envolvendo eletrodeposição - Parte 1: Célula de Hull padrão; e DIN 50957-2:2019-06, Teste de eletrólitos usados ??para revestimentos metálicos eletrodepositados - Teste envolvendo eletrodeposição - Parte 2: Células de teste especiais – normas em alemão. Há diversos formatos de Células de Hull com capacidade para diferentes volumes de eletrólito, sendo comum o uso da célula de 250ml (267ml), ilustrada na figura 3.
Figura 3 – Distribuição da corrente contínua convencional na Célula de Hull
As dimensões internas da Célula de Hull são: a) 48mm; b) 102mm; c) 127mm; d) 64mm; profundidade de 65mm, construídas geralmente em plástico PMMA, PP, PEAD, PTFE, PVC, resinas epóxi, PU laminadas, cerâmica e vidro.
A equação geral de Hull (1), usada para calcular a densidade de corrente na Célula de Hull em qualquer ponto, é:
CD = I.(C1 – C2 log L)
equação (1)
Onde: CD - Densidade de corrente (A/dm2); I - Intensidade de corrente aplicada (A) ; L - Distância a partir da borda do lado de alta densidade de corrente na placa do cátodo (distância em cm em qualquer ponto da placa pra uma determinada região analisada em relação ao lado de maior densidade de corrente do cátodo); C1 e C2 - são constantes dependentes da natureza dos diferentes tipos de eletrólitos, obtidas por R.O. Hull.
NOHSE et al (1966) citam em sua obra que Hull determinou essas constantes para um número de eletrólitos e descobriu que, em geral, os valores se alteraram pouco de um eletrólito para outro, em consequência, os valores médios foram calculados e são aplicáveis a todos os eletrólitos através da equação (2), para a célula de 250ml (267 ou 534ml):
CD = I.(5,10 - 5,24 log L)
equação (2)
E para a célula de 1000ml é utilizada a equação (3) a seguir:
CD = I.( 3,46- 3,045 log L)
equação (3)
A Tabela 1, a seguir, mostra os valores da densidade de corrente (CD) em A/dm2 obtidos na equação de Hull (2) em função da distância de determinados pontos (L) ao longo do cátodo, para intensidades de corrente total (I) variando de 1 a 5 A.
Tabela 1 - Variação da densidade de corrente na Célula de Hull 250ml (267 ou 534ml) em diferentes pontos do cátodo em função da distância para determinada intensidade de corrente de 1 a 5A.
É comum o uso de uma escala contendo alguns valores arredondados da tabela acima com densidade de corrente para diferentes regiões do cátodo, permitindo a rápida visualização dos resultados obtidos no ensaio com a Célula de Hull, conforme a figura 4.
Figura 4 - Escala para Célula de Hull V = 250 – (267 ou 534ml) com distâncias de 0-10 cm – Desenho autoral.
Observe que os valores indicados na escala da figura 4 são teóricos de acordo com a equação de Hull (2); para os ensaios na Célula de Hull dependem da precisão no ajuste da corrente no retificador usado, logo, pequenas alterações devem ser consideradas dependendo do tipo de equipamento para cada eletrólito ensaiado.
Células com canal de insuflação de ar ou recirculação do eletrólito, bem como inserção de resistência de aquecimento para testes com temperaturas específicas, são ideais quando há diversos processos galvânicos – que operam em condições de temperatura diferenciada – a serem ensaiados.
O que é possível inferir no ensaio com a Célula de Hull
A Célula de Hull permite obter resultados quantitativos e qualita-tivos de qualquer processo de eletro-deposição, também é especialmente utilizada para otimizar a densidade de corrente, a concentração de aditivos, indicar o nível do teor dos sais, mostrar contaminações (inorgânicas e orgânicas), bem como planejar a mitigação dessas contaminações e indicar capabilidade de macro-throwing power na célula longa.
A Célula de Hull com cátodo plano não é usada para determinar e comparar throwing power de processos galvânicos, isso é feito usando a Célula de Hull com cátodo rotativo ou, especialmente, a Célula de Haring-Blum, que foi desenvolvida para essa finalidade. A tabela 2 mostra os principais usos da Célula de Hull.
Tabela 2 – Usos da Célula de Hull
A figura 5, a seguir, ilustra o conjunto completo ideal para o controle da qualidade e análise dos custos energéticos em processos galvânicos através dos ensaios em Célula de Hull, usando retificador com tempo programável e informações de Ah, Wh, W, I, V, t, °C, Célula de Hull com aquecimento e insuflação de ar através de compressor de diafragma ou recirculação do banho através de bomba peristáltica.
Figura 5 – Conjunto completo, fornecido pela PA8, para pesquisa dos custos da energia elétrica nos processos galvânicos e outros ensaios em Célula de Hull.
Considerações importantes sobre a Célula de Hull
De acordo com SCHMIT et al (2021), nos anos de 2017 e de 2018, a DIN 50957, ‘Teste de banhos de galvanoplastia, teste de galvanoplastia com a Célula Hull’, foi verificada rotineiramente pelo comitê DIN NA 062-01-61 AA e ajustada em relação a novas descobertas. Isso envolveu uma dicotomia desse padrão. A DIN 50957-1:2016-02, Parte 1: ‘Célula de Hull padrão’, baseia-se essencialmente na DIN 50957:1978 e descreve a Célula de Hull 250ml (267 ou 534ml). A DIN 50957-2:2019, Parte 2: ‘Células de teste especiais, inclui, em particular, uma versão da Célula Hull que é mais longa que a célula padrão (referida como célula longa) e tem folhas de cátodo em ângulo adicional. Como parte do processamento de DIN 50957-1 e -2, foram realizadas simulações para a distribuição de densidade de corrente primária e secundária dessas duas Células de Hull com o programa de simulação COMSOL Multiphysics® (módulo eletroquímico). Além disso, as simulações foram comparadas com investigações experimentais. Pode-se demonstrar, por meio de uma simulação, que são obtidas curvas de densidade de corrente muito mais rápidas, por exemplo, com mudanças de geometria das Células de Hull.
Os resultados obtidos nos ensaios com a Célula de Hull usam simbologia gráfica, de acordo com a norma DIN 50957-1:2016-02, em seus relatórios, para expressar aspectos do revestimento obtidos nas condições da amostra em estudo, conforme figura 6, a seguir:
Figura 6 – Representação gráfica dos aspectos do revestimento ensaiado conforme noma DIN 50957-1:2016-02.
Exemplo de aplicação da Célula de Hull na galvanoplastia
A seguir é demonstrado um método prático para avaliar e controlar processos de zinco alcalino sem cianeto usando Célula de Hull.
Materiais necessários e condições de trabalho:
- Célula de Hull 250ml;
- 250ml de amostra do banho de zinco alcalino sem cianeto;
- Anodo de zinco (opcionalmente, pode-se usar anodo de aço carbono niquelado para melhor reproduzir a operacionalização na produção, mas recomenda-se a realização de ensaios comparativos com ambos os anodos (solúvel e insolúvel) antes de adotar o procedimento);
- Cátodo de ferro;
- Balança analítica;
- Temperatura ambiente (de preferência usar a temperatura média do tanque de produção na linha galvânica);
- Sem agitação a ar (circulação por bomba peristáltica na vazão de 100ml/minuto, usando Célula de Hull especial, pode-se produzir melhores resultados do que na condição estática, sem agitação);
- 2 amperes, 30 minutos (nessa condição, a velocidade de deposição da camada, média teórica, é de 0,26 µ/minuto e a massa de zinco média – a ser depositada no intervalo de tempo do ensaio – é de 0,554g/dm2);
- Pesar o cátodo (desengraxado e seco) em balança analítica antes do ensaio e depois de depositar o zinco e anotar as respectivas massas para o cálculo de rendimento do processo.
O ensaio objetiva depositar camada de zinco no cátodo da Célula de Hull, com intensidade de corrente de 2 A durante 30 minutos, e, posteriormente, avaliar a distribuição da camada e sua espessura obtida no painel zincado, que não deve ser ativado, lavado e seco após a deposição.
Medir a camada de zinco depositada na Célula de Hull nos pontos localizados (conforme as distâncias dos círculos em vermelho na figura 7), ilustrados no cátodo com a escala de Hull sobreposta, para intensidade de corrente no retificador 2 A, respectivamente (alta densidade de corrente - ADC), em 8 A borda esquerda, (baixa densidade de corrente - BDC) em 0,4 A na borda direita, conforme Figura 7.
Figura 7 – Posicionamento do cátodo sobre a escala para avaliar o resultado de um revestimento após ensaio na Célula de Hull.
Após a medição de camada nos pontos 8 A (ADC) e 0,4 A (BDC), calcular a relação de aditivos através da equação (4):
Relação de aditivos = ADC/BDC
equação (4)
O resultado da relação deve estar na faixa entre 1,5 e 2,25. Valor abaixo de 1,5 indica alta concentração de aditivos abrilhantadores, valor acima de 2,25 indica falta de aditivos abrilhantadores.
O cálculo de rendimento do processo para esse ensaio pode ser obtido de acordo com a equação (5) a seguir:
equação (5)
O teste serve para avaliar o rendimento do processo e o conteúdo de aditivos abrilhantadores, entretanto, é preciso considerar os teores de metal, hidróxido e carbonato(1) (limite de 70g/L para Na2CO3 e de 90g/L para K2CO3) fora de concentração de trabalho; contaminação com cromo; temperatura elevada acima da faixa média; filtração insuficiente no tanque de trabalho; excesso de aditivo purificador; e contaminação orgânica; pois todos esses afetam os resultados do teste.
Antes de executar o teste acima é ideal efetuar a análise química da amostra para confrontar com resultados registrados de eletrólitos em concentração padrão de trabalho.
Recomenda-se arquivar padrões físicos e de imagens do ensaio em Célula de Hull, pois eles ajudam a construir a base de conhecimento para operacionalização do processo.
Considerações importantes sobre o processo de zinco alcalino sem cianeto
Entre os tipos de eletrólitos de zinco (cianídrico, ácido e alcalino), o zinco alcalino, sem cianeto, é o que reúne melhores atributos: ecologicamente correto em relação à toxidade e de fácil mitigação de resíduos; permite depósitos em aços temperados, ferro fundido, aços de baixo carbono; baixo custo de montagem; baixa corrosividade da solução; boa condutividade; fácil de operar e controlar; facilidade na lavagem; ótima velocidade de deposição; excelente throwing power; bom poder de cobertura; ótima ductilidade; boa adesão; ótima aparência – brilhante espelhado – em todas as faixas de densidade de corrente; excelente receptividade de cromatos; boa proteção à corrosão (superior aos outros tipos de eletrólitos de zinco).
No gráfico 1, adaptado de SILVA et al, 2006, observa-se o comportamento do rendimento catódico do eletrólito de zinco alcalino sem cianeto, à temperatura ambiente, iniciando-se com o melhor rendimento na faixa até 2 A/dm2, e declinando à medida que ocorre aumento da densidade de corrente até 8 A/dm2.
Gráfico 1 – Rendimento catódico % do eletrólito de zinco alcalino SCN.
O que usar no zinco alcalino SCN: base alcalina de sódio ou de potássio?
O uso de hidróxido de potássio (KOH) em vez de hidróxido de sódio (NaOH) proporciona maior condutividade. Para uma solução 3N, a condutividade do KOH é 29,63% maior do que a do NaOH, resultando em menor consumo de energia elétrica na eletrólise uma vez que o aumento da condutividade do eletrólito requer menor tensão necessária para obter a mesma corrente na eletrólise, consequentemente, produzindo menor aquecimento do banho.
Outra vantagem de usar sais de potássio reside na maior facilidade de lavagem das peças devido à maior solubilidade do carbonato de potássio presente no banho – sua saturação é 2,6 vezes maior que a do carbonato de sódio.
A desvantagem, quando se usa sais de potássio, é que o carbonato de potássio formado não pode ser cristalizado sob resfriamento devido sua elevada solubilidade, portanto, a sua remoção deve ser feita por outro método ou por diluição do banho, além de que o custo do eletrólito à base de potássio é maior devido ao preço do metal alcalino.
Em relação à comparação entre o throwing power e a eficiência catódica entre sódio e potássio, para ambos, é semelhante.
A decisão de usar potássio deve ser estudada com bases experimentais para cada aplicação, principalmente, porque a maioria dos atuais sistemas de zinco alcalino sem cianeto em uso no mundo é à base de sódio.
O processo de zinco alcalino sem cianeto geralmente usa aditivos proprietários:
Parte A – Solução base utilizada na montagem e manutenção;
Parte B – Abrilhantador promotor de nivelamento e throwing power em baixa densidade de corrente utilizado na montagem e manutenção;
Parte C – Condicionador utilizado na montagem e manutenção;
Parte P – Purificador utilizado na montagem e manutenção;
Parte S – Supressor de gases utilizado na montagem e manutenção, ideal para instalações que não tem exaustão e lavador de gases.
As principais características operacionais do eletrólito de zinco alcalino sem cianeto estão na tabela 3.
Tabela 3: Principais características operacionais do eletrólito de zinco alcalino sem cianeto.
Nota (1)
Carbonatos de sódio e de potássio - Nota (1)
O carbonato de sódio (Na2CO3) e o carbonato de potássio (K2CO3) são formados durante o uso do eletrólito – e também durante a inatividade durante longo período. Não é recomendável adicionar carga inicial de carbonato de sódio ou de potássio na montagem de um banho novo por questão de economia, o limite de trabalho é de até 70g/L para Na2CO3 e de 91 g/L para K2CO3 e requer eliminação se estiver acima.
O carbonato de sódio ou de potássio são formados pela adsorção do dióxido de carbono da atmosfera, pelo hidróxido de sódio, ou pelo hidróxido de potássio na solução eletrolítica. Se a solução for agitada com ar, isso aumentará a taxa de adsorção. Da mesma forma, a turbulência excessiva de um sistema de filtragem aumentará a concentração de carbonatos.
Para eliminar carbonato de sódio pode-se resfriar a solução até 6 °C; assim, o carbonato cristaliza na superfície do banho e sua remoção pode ser feita mecanicamente (necessita de posterior filtração do eletrólito de zinco).
No caso do carbonato de potássio, devido à sua elevada solubilidade, ele não cristaliza em baixas temperaturas e sua remoção ‘mais econômica’ é por diluição do banho.
Em concentrações de carbonatos superiores ao limite de trabalho, a penetração torna-se deficiente e ocorre diminuição da eficiência catódica e depósitos escuros/queimados são resultantes.
Resultados experimentais, publicados por SILVA et al, 2006, obtidos por voltametria de varredura linear, demonstram que há influência da concentração de Na2CO3 entre 5,0 a 30 g/L na reação de desprendimento de hidrogênio durante o processo de eletrodeposição, e há o aumento da concentração de Na2CO3 no eletrólito deslocado, sobre o potencial da reação de desprendimento de hidrogênio para valores mais negativos no intervalo de 5 a 30 g/L, cessando para concentrações de carbonato superiores a 30 g/L. Assim, conclui-se que o Na2CO3 contribui para o aumento do rendimento catódico pela redução do desprendimento gasoso.
No mesmo estudo, foi observado que a presença do carbonato no eletrólito levou à formação de depósitos mais brilhantes em toda a região de densidade de corrente selecionada, além de ele permitir estabelecer a otimização da concentração de carbonato de sódio entre 25 e 30 g/L como ideal em ensaios de Células de Hull.
Conclusão
Desde a sua invenção, há mais de 88 anos, a Célula de Hull desperta, tanto no meio acadêmico quanto no meio industrial, interesse em pesquisa e desenvolvimento de processos, bem como surgem variantes de sua forma primitiva como fruto das muitas investigações que continuam a ser patenteadas. Fato é que a Célula de Hull primitiva é a mais econômica e poderosa ferramenta para o controle da qualidade dos processos galvanotécnicos, pois, além de requerer pouco investimento quando comparada a outras técnicas analíticas de investigação da eletroquímica, permite simular parâmetros de controle dos ‘banhos galvânicos’; sendo, ainda, acessível a qualquer tamanho de empresa – muitas vezes utilizada ao lado dos tanques de trabalho usando o próprio retificador da instalação.
Interpretar resultados obtidos nos ensaios com Célula de Hull, longe de apenas demonstrar graficamente a simbologia conforme a norma DIN 50957-1:2016, oferece oportunidade para a criatividade e aprendizagem para atingir o domínio da galvanotécnica e estabelecimento de processos sustentáveis.
Agradecimento
Agradeço a gentileza, prontidão e colaboração do Sr. Harry F. Hull pela cessão e autorização de uso da fotografia e informações biográficas de seu pai, o Engenheiro Químico Richard Ostrander Hull, compartilhando memórias de sua família e da Célula de Hull.
Referências
HULL, R.O; US Patent nº 2,149,344 – Apparatus and process for study of plating solutions, March, 7, 1939, USA, 8p. Disponível em: https://www.mcgean.com/About-McGean/Our-History. acesso em 16/02/2023
NOHSE, W; HEYES, J; WAGENBLAST, G. The Hull Cell. Teddingtonn, England. Edited by Electroplating and metal finishing, 2ª Ed. chap. 2, p.17-25, 1966.
Norma técnica DIN 50957-1:2016-02. Teste de eletrólitos usados para revestimentos metálicos eletrodepositados - Teste envolvendo eletrodeposição - Parte 1: Célula de Hull padrão. 2016, Alemanha, 14p.
Norma técnica DIN 50957-2:2019-06. Teste de eletrólitos usados ??para revestimentos metálicos eletrodepositados - Teste envolvendo eletrodeposição - Parte 2: Células de teste especiais. 2019, Alemanha, 25p.
SCHIMIT, Udo; PEIPMANN, Ralf; BUND, Andreas. Zweidimensionale Simulation von Hull-Zellen, 2021. Disponível em:
https://www.leuze-verlag.de/fachzeitschriften/galvanotechnik/itemlist/user/4521-drudoschmidt?dt=1675524698971. Acesso em 04/02/2023
SILVA et all. Quim. Nova, Vol. 29, N° 1, 2006, 15-19.
*Pedro de Araújo é Consultor Galvanotécnico e Ambiental com 41 anos de experiência, professor, autor, pesquisador autônomo e inventor, Pós-Graduado Latu-Sensu em Auditoria e Perícia Ambiental – Unicesumar – Maringá-PR. Pós-Graduado em MBA em Gestão Ambiental e Desenvolvimento Sustentável - Unicesumar – Maringá-PR. Tecnólogo em Gestão Ambiental – Unicesumar – Maringá-PR. Técnico Químico – ETECAP-Campinas-SP. Comanda a PA8 Consultoria e Mentoria Galvanotécnica e Ambiental