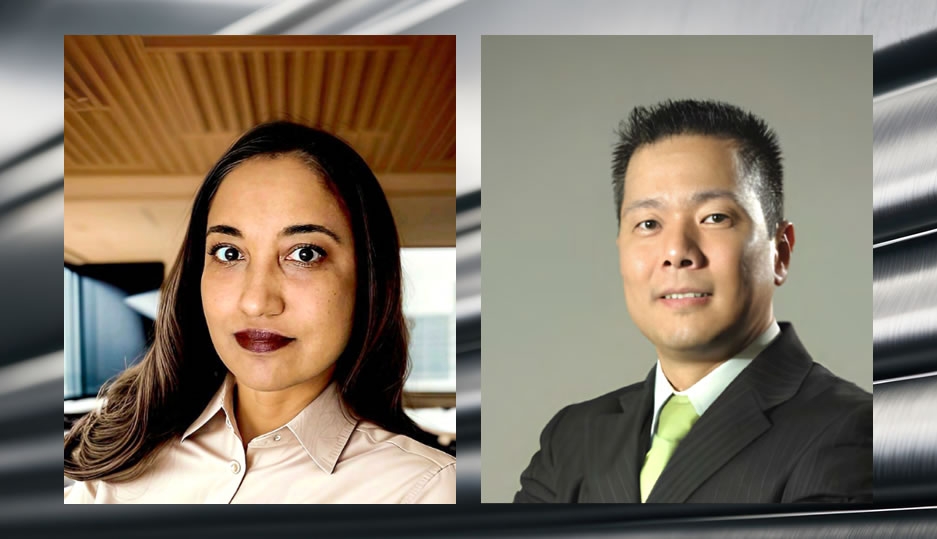
Patrícia Silva
Consultora de Negócios da BASF | CHEMETALL
patricia-cristiane.da-silva@basf.com
Roger Azeka
Gerente Laboratório Tecnológico da BASF Chemetall
roger.azeka@basf.com
Detalhamento dos processos e revestimentos para utilização em alumínio, incluindo suas aplicações, etapas, e certificações que asseguram acabamentos de alta qualidade nos produtos.
A escolha do tratamento superficial é definida de acordo com a utilização do produto acabado e a necessidade de resistência à corrosão, podendo ser protetiva ou decorativa. Sua principal função é proteger a superfície metálica dos agentes causadores da corrosão, que podem ser:
- Atmosfera: Umidade, sais em suspensão (especialmente orla marítima), gases industriais (exemplo: enxofre), poeira, etc.
- Solos: Umidade e sais minerais, podendo também apresentar características ácidas ou básicas.
O sucesso do acabamento não depende exclusivamente da qualidade do revestimento e características técnicas, mas também, fundamentalmente, do estado e preparo das superfícies em que serão aplicadas.
Acrescenta-se a isso o fato de que muitas pessoas que vão utilizar esses produtos apresentam um desconhecimento justificável, levando-os, por vezes, a resultados pouco produtivos e inadequados para o fim a que se destinam.
O processo de preparação de superfícies
O processo de preparação de superfícies foi revolucionado, tendo como impulsionadores objetivos ambiciosos em matéria de proteção climática, ecoeficiência e produtos químicos seguros. Aumentando o desempenho do processo através da utilização de métodos avançados de investigação analítica, espécies químicas personalizadas e técnicas eletroquímicas preditivas.
Realizar tratamento sobre substrato de alumínio é um tópico de muito tempo atrás, mas que continua em desenvolvimento até os dias atuais.
Em 1857, foi descoberto, por H. Buff e C. Pollack, a tendência de o alumínio recobrir-se de óxido em uma célula eletrolítica, colocando o alumínio como anodo. Baseadas nesta descoberta, inúmeras pesquisas foram feitas, mas, somente por volta de 1909, foram desenvolvidos os princípios básicos para a oxidação eletrolítica em meio sulfúrico.
Posteriormente, inúmeras patentes e aperfeiçoamentos, a nível industrial, surgiram em diversos países, sendo a mais importante patenteada com o nome de ‘Aluminite’ (marca americana da ‘Aluminium Colors’), desenvolvida por Henry Herbert Gower e Thomas Henry Rowatt, em 1910, que coligaram a anodização em meio sulfúrico com o tingimento do alumínio.
Em 1923, Bengough e Stuart, na Inglaterra, desenvolveram, a nível industrial, a anodização em meio crômico. Posteriormente, os japoneses Setoh Rikagu e Meyata Kenkyugo colocaram em prática a anodização em meio oxálico, aperfeiçoada por Kuttre, na Alemanha, sendo patenteada com o nome de ‘Eloxal’.
Atualmente, a maior parte das patentes de anodização são de domínio público.
Mercado de Alumínio
O alumínio é um metal branco prateado leve, o elemento metálico mais abundante na crosta terrestre e o metal não ferroso mais utilizado.
A opção de escolha do alumínio para tantas áreas diferentes pode ser entendida quando compreendidos os benefícios desse metal. E são muitos, pois trata-se de um metal leve, que apresenta elevadíssima resistência à corrosão na temperatura ambiente, possui excelente condutividade térmica e uma relação muito favorável entre condutividade elétrica e peso específico. Além de não ser magnético, seu preço é mais competitivo em comparação a outros metais, por ser abundante na natureza, e é também um metal especialmente indicado para conservação de alimentos e bebidas.
As aplicações incluem telhados, isolamento de folhas, janelas, revestimentos, portas, fachadas de lojas, balaustradas e ferragens arquitetônicas. O alumínio também é comumente usado na forma de placas de soleira e pisos industriais.
O mercado de alumínio é segmentado por tipo de processamento, indústria de usuário final e geografia. Por tipo de processamento, o mercado é segmentado em fundidos, extrusões, forjados, produtos laminados planos, e pigmentos e pós. A indústria de usuário final segmenta o mercado em indústrias automotiva, aeroespacial e de defesa, construção civil, elétrica e eletrônica, embalagens, industrial e outras.
Além de todas essas qualidades relacionadas aos benefícios do metal, existe uma que merece destaque: a sustentabilidade. Sem dúvida, esse aspecto torna o alumínio e sua utilização intensiva muito mais atrativa, desde a exploração do minério (no qual se faz uma planejada rotação na exploração das minas com o respectivo reflorestamento após o esgotamento) até o seu elevado índice de reciclagem.
Com um índice superior ao da média mundial, o Brasil recicla cerca de 38,5% de todo o consumo doméstico, conforme apontam dados da Associação Brasileira do Alumínio - ABAL. O alumínio é infinitamente reciclável, e 75% desse metal existente no mundo ainda não foi disponibilizado para reutilização.
No setor automobilístico, a cada ano, o alumínio é considerado como matéria-prima essencial e importante. Nas últimas décadas, surgiu um movimento mundial muito forte para reduzir a emissão de CO2 proveniente do consumo de combustível, já que o gás contribui para o efeito estufa, e, consequentemente, para o aquecimento global.
De acordo com uma pesquisa da The Aluminum Association, a cada 10% de redução no peso do automóvel, há o aumento de 5% a 10% de eficiência do combustível. O levantamento também mostrou que a cada 1 kg de redução da massa do carro, há uma diminuição de 20 kg de gás estufa durante toda a vida útil do automóvel. Antes de o alumínio entrar na produção de automóveis, o material dominante era o aço. A substituição veio em razão de o aço ser muito pesado – enquanto o alumínio apresenta densidade de 2,7 g/cm³, materiais ferrosos possuem, em média, 7,8 g/cm³.
Anodização
O alumínio apresenta formação natural de uma película de óxido de alumínio (Al?O?), sendo reativo a ácidos de álcalis com evolução de hidrogênio. Para aumentar a resistência à corrosão e ao desgaste, submete-se o alumínio a um processo eletroquímico conhecido como anodização.
A anodização é um processo eletrolítico ou eletroquímico que consiste em tornar mais espesso esse óxido por meio da aplicação de um potencial ou corrente anódica ao metal para a formação de uma camada, que vai desde porosa até extremamente dura, à camada anódica.
Figura 1: Fluxograma Geral de Processo de Anodização
Na etapa principal onde ocorre a anodização, utilizamos um eletrólito (aqui utilizaremos como exemplo o ácido sulfúrico), um gerador de corrente contínua (retificador), formamos uma pilha com catodo (polo negativo, que deve ser de material resistente ao meio ácido, tal como chumbo ou alumínio) e o anodo (polo positivo: alumínio a ser processado).
Ao aplicar a corrente elétrica contínua, ocorrerá a eletrólise. No anodo (peça de alumínio), haverá a eletrólise do ácido, liberando o oxigênio que reagirá com o alumínio, transformando sua superfície em óxido de alumínio (alumina). Essa película de alumina, além de fornecer uma excelente proteção contra a corrosão, é extremamente dura, transparente, anidra, e porosa. Sua espessura aumenta proporcionalmente ao tempo e à exposição no eletrólito.
Figura 2: Reações durante o processo de anodização
A reação do alumínio com o oxigênio é altamente exotérmica, por isso adapta-se ao sistema de refrigeração, mantendo uma temperatura constante (± 1,5°C). Para haver uma melhor uniformidade de temperatura no eletrólito, faz-se uma agitação por injeção de ar.
Figura 3: Ilustração esquemática do processo de formação da camada anodizada, incluindo configuração de célula eletroquímica e curva de densidade de corrente-tempo e potencial-tempo, típicas do processo de anodização do alumínio e suas ligas. Estágios de crescimento dos poros:
- Formação da camada de óxido
- Formação de poços por heterogeneidades locais de campo elétrico
- Formação inicial de poros
- Crescimento dos poros em condições de estado estacionário.
Figura 4: Formação da Camada Barreira
Se oxidarmos uma peça de alumínio em um eletrólito que não tenha ação dissolvente sobre a camada de alumina, observa-se que a intensidade da corrente para uma tensão determinada diminui muito rapidamente até tornar-se nula.
Figura 5: Gráfico tensão por tempo
Se invertemos o sentido da corrente, sua intensidade retorna ao seu valor inicial elevado e permanece constante. Assim, a célula de alumina funciona como um retificador de corrente. Temos então a formação de uma camada de alumina, contínua e compacta, que impede a passagem de corrente elétrica, à qual chamamos de camada-barreira. A espessura desta película representa a distância que um íon metálico pode alcançar, através de seu próprio óxido, sob a influência de um dado potencial.
Figura 6: Exemplo de estrutura da camada de óxido
Quando se oxida uma peça de alumínio em uma solução que tenha uma ação dissolvente sobre a camada de alumina, observa-se que a intensidade de corrente, para uma tensão determinada, diminui muito rapidamente, como anteriormente, porém, se estabiliza em seguida a um nível mais elevado. A camada de óxido formada se constitui de células hexagonais sobrepostas, que será de alumina amorfa, pouco resistente aos ácidos, e a periferia será formada de alumina cristalina muito resistente aos ácidos. Aparecem, então, na superfície da camada-barreira, milhares de pontos de ataque, que são consequência do efeito da dissolução de película pelo eletrólito, que se produz no centro das células de alumina e que constitui o começo dos poros.
Figura 7: Película anódica no princípio de sua formação em um eletrólito com ação dissolvente sobre a camada de alumina.
Figura 8: Estudos sucessivos do progresso da película anódica a partir de um poro isolado.
Principais Propriedades da Película Anódica (Alumina)
Dureza
Pela sua natureza, a alumina é extremamente dura, sendo pouco menor que o diamante, variando no sentido inverso à sua porosidade. A dureza da alumina atinge entre 7 e 8 na escala de Mohs, igualando-se ao quartzo e ao topázio.
Resistência Elétrica
A alumina é um isolante elétrico de qualidade superior à da porcelana.
Porosidade
A película anódica (alumina), obtida em meio sulfúrico a 20 volts, em 1 cm², produz aproximadamente 50 mil poros, e, em meio crômico a 40 volts, cerca de 8 mil poros.
Anodização em Meio Sulfúrico
É o processo anódico mais utilizado, constituindo-se de ácido sulfúrico, cujo custo é muito baixo, além de fácil comercialização. Em função da temperatura e tensão, apresenta uma versatilidade incrível quanto à qualidade da camada formada, desde películas porosas – com grande facilidade de tingimento – até películas extremamente duras, utilizadas para fins técnicos.
Eletrólito em meio Sulfúrico
Vantagens:
- Resistência aumentada à corrosão;
- Melhor aderência para pintura e adesivos;
- Aspecto estético melhorado com várias opções de cores.
Sistema Qualicoat
O Qualicoat é uma certificação internacional para sistemas de revestimento em alumínio. Ele garante que os processos de pintura eletrostática atendam a altos padrões de qualidade e durabilidade.
História e Origem
A Qualicoat é uma organização internacional dedicada a garantir a qualidade dos revestimentos de alumínio através de normas rigorosas e processos de certificação. Fundada na Europa, em 1986, a associação é formada por representantes da indústria de revestimento de alumínio para padronizar a qualidade dos acabamentos aplicados a produtos de alumínio. Desde então, a organização cresceu e se tornou um marco mundial em qualidade, com um conjunto de especificações técnicas atualizadas regularmente para atender às crescentes demandas tecnológicas e ambientais.
Objetivos da Qualicoat
Os principais objetivos da Qualicoat incluem:
I. Garantia de Qualidade: Fornecer normas que assegurem a produção de revestimentos de alta qualidade.
II. Consistência de Produção: Promover a uniformidade da qualidade em todas as produções de alumínio revestido.
III. Inovação e Desenvolvimento: Melhorar continuamente as técnicas de revestimento e seus impactos ambientais.
Principais pontos de avaliação para certificação
a. Preparação da Superfície
A superfície de alumínio deve ser adequadamente tratada antes da aplicação do revestimento para garantir a aderência e durabilidade do acabamento. Todos os pré-tratamentos químicos para revestimentos orgânicos em pó e líquidos devem incluir uma etapa de perda de massa do alumínio, que consiste em uma ou mais etapas.
Sistema Qualanod
O Qualanod é uma certificação específica para o processo de anodização de alumínio, garantindo que os produtos anodizados atendam a rigorosos padrões de qualidade e desempenho.
Conclusão
Os sistemas de tratamento de superfície sobre alumínio e as certificações Qualicoat e Qualanod são elementos cruciais para assegurar acabamentos de alta qualidade em produtos de alumínio. Cada um oferece vantagens específicas que, quando combinadas, garantem não apenas a proteção, mas também a estética e a longevidade dos materiais. A adesão a esses processos e certificações é fundamental para os fabricantes que buscam excelência e inovação em seus produtos.
Referências
- ABAL – Tratamento de Superfície do Alumínio e suas Ligas – 2021
- Artigo: O Processo de Anodização e suas ligas: uma abordagem histórica e eletroquímica – Sociedade Brasileira de Química – Revista Química Nova. Publicação por João Victor de Sousa Araujo, Regiane Maria Pereira da Silva, Rafael Emil Klumpp e Isolda Costa – USP
- Qualicoat Site – www.qualicoat.net: Specifications for a quality label for liquid and powder coatings on aluminium for architectural applications
- Qualicoat Specifications 2024 – Specification WG – Pascale Bellot