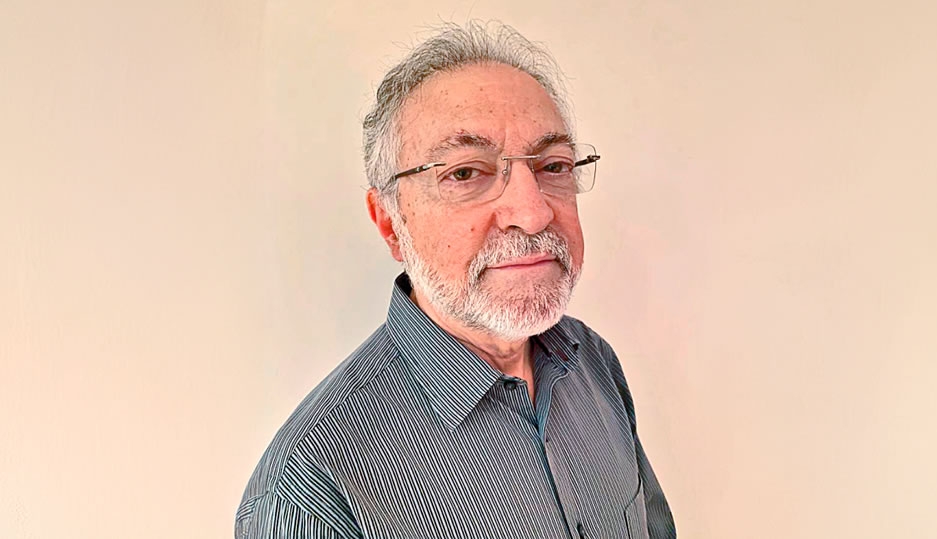
Anuar Gazal, Consultor Técnico da Produtos Químicos Quimidream Ltda
Conheça os tipos, finalidade, recobrimentos químicos empregados e os aspectos mecânicos dos elementos de fixação
Em qualquer utilização, por mais simples que ela seja, é necessário fazer a união de peças entre si. Para isso, em mecânica, há a exigência de elementos de fixação. Portanto, os elementos de fixação têm como objetivo principal unir duas ou mais peças de forma fixa ou móvel em projetos mecânicos. Esses fixadores possuem aplicações e funções diferenciadas, onde alguns visam à fixação permanente e outros permitem até a rotação de peças com segurança.
De forma bem geral, os elementos de fixação mais comuns em mecânica são: rebites, pinos, cavilhas, parafusos, porcas, arruelas, chavetas, entre outros.
Pensando em uma divisão bem simples em relação ao tipo de fixação, encontra-se a fixação móvel e a fixação permanente. A fixação móvel permite que os elementos de fixação sejam colocados ou retirados do conjunto sem causar nenhum dano às peças. Como exemplo disso têm-se os parafusos, as porcas e as arruelas. Já a fixação permanente não permite essa flexibilidade, uma vez instalados, os elementos de fixação não podem ser reutilizados, pois ao serem retirados perdem sua utilização. É o exemplo de rebites e soldas.
De qualquer forma, tanto os elementos de fixação móvel quanto permanente exigem um manuseio feito com muita habilidade, pois são considerados os componentes mais frágeis da máquina. Assim, isso requer um projeto adequado ao conjunto mecânico destinado, pois de nada adianta utilizar elementos de fixação fracos para peças robustas. Sem contar que se deve pensar nas tensões exercidas pelas peças para que não haja rupturas.
Principais tipos de elementos de fixação
- Rebite: Formado por um corpo cilíndrico e uma cabeça, é fabricado em aço, alumínio, cobre ou latão. É usado para a fixação permanente de duas ou mais peças.
- Parafuso: É uma peça formada por um corpo cilíndrico e uma cabeça, que pode ter várias formas. É utilizado na união não permanente das peças. Os parafusos se diferenciam pela forma de rosca, da cabeça, da haste e do tipo de acionamento. As roscas encontradas nos parafusos permitem a união e a desmontagem das peças. Os filetes das roscas apresentam diversos perfis uniformes, que dão nome às roscas. O tipo de acionamento está relacionado com o tipo de cabeça do parafuso. O corpo do parafuso pode ser cilíndrico ou cônico, totalmente roscado, ou apenas parcialmente. Essas diferenças, determinadas pelas funções dos parafusos, permitem classificá-los em quatro categorias: parafusos passantes; parafusos não passantes; parafusos de pressão; e parafusos prisioneiros.
- Pino: O pino é utilizado para poder disponibilizar movimento de rotação em uma das peças, além de alinhar e fixar os elementos. Os pinos são usados em junções resistentes a vibrações.
- Cavilha: A cavilha une peças que não são articuladas entre si e, assim como os pinos, também servem para alinhar e fixar os elementos das máquinas.
- Contrapino ou Cupilha: Este elemento de fixação é uma haste ou arame com forma semelhante a um meio cilindro, porém, dobrado de modo a formar uma cabeça e duas pernas desiguais.
- Porca: É formada por um furo roscado, o qual serve para atarraxar o parafuso. A porca pode ter formato de prisma, de cilindro, etc.
- Arruela: É um disco metálico com um furo no centro. Esse furo permite que o corpo do parafuso passe por dentro da arruela.
Coeficiente de Atrito
O coeficiente de atrito é uma medida adimensional que expressa a oposição que mostram as superfícies de dois corpos em contato ao deslizar um em relação ao outro. Geralmente é representado com a letra grega μ (mi). Em análise dimensional, uma grandeza adimensional ou número adimensional é um número desprovido de qualquer unidade física que o defina; portanto, é um número puro. O valor do coeficiente de atrito é característico de cada par de materiais, e não uma propriedade intrínseca do material. Depende de muitos fatores, tais como o acabamento das superfícies em contato, a velocidade relativa entre as superfícies, a temperatura, etc.
Geralmente distinguem-se dois valores:
- Coeficiente de atrito estático (μe): É medido quando ambas as superfícies estão em repouso (sem se mover).
- Coeficiente de atrito dinâmico (μd): É medido quando uma ou ambas as superfícies estão em movimento (podem mover-se apenas uma ou as duas).
O coeficiente de atrito dinâmico (μd) é sempre menor que o coeficiente de atrito estático (μe). Podemos dizer que as forças de atrito são inevitáveis no nosso cotidiano. Caso não conseguíssemos vencê-las, elas fariam com que todos os objetos que estivessem em movimento, em todas as direções, parassem. Por outro lado, se não tivesse atrito, os carros não poderiam andar e nós não poderíamos sequer segurar um lápis para escrever. Podemos dizer que, sem o atrito, um prego seria inútil. Assim, podemos afirmar que atrito são forças de contato entre duas superfícies.
Na figura abaixo, temos um livro em repouso sobre uma mesa. Atuando sobre ele há somente a força gravitacional (Fg) que está equilibrada com a força normal (FN). Caso exerçamos sobre ele uma força F, tentando movê-lo para a esquerda, em resposta, surge uma força de atrito fs para a direita, que equilibra a força que aplicamos. Chamamos essa força de força de atrito estático (fs). O livro permanece imóvel.
Entretanto, à medida que vamos aumentando a intensidade da força aplicada sobre o livro, de modo que ele comece a se movimentar, sofrendo uma aceleração para a esquerda, a força de atrito que se opõe ao movimento nessa nova situação é chamada de força de atrito cinético (fc).
Assim, podemos dizer que a intensidade da força de atrito cinético (fc), que atua sobre corpos que estão se movendo, é menor do que a intensidade máxima da força de atrito estático (fs), que atua sobre objetos em repouso. Podemos, então, determinar tanto o módulo da força de atrito estático quanto o módulo da força de atrito cinético. As forças de atrito dependem da força normal e do coeficiente de atrito. Dessa forma, temos:
Onde:
- μs é o coeficiente de atrito estático; e
- μc é o coeficiente de atrito cinético.
Não podemos nos esquecer de que os coeficientes μs e μc são adimensionais, ou seja, não possuem unidade de medida. Nas indústrias automotivas, o processo de aperto dos parafusos (por exemplo, cabeçote + bloco do motor) é controlado por uma força tensora, que pode ser calculada pela seguinte fórmula: MA = Fv. d. k
Onde: MA = Torque (total de aperto) ... Nm Fv = Força Tensora ... kN d = Diâmetro nominal do elemento de fixação ... mm K = Coeficiente ou fator de torque ... (adimensional)
Considerando os diversos revestimentos e materiais normalmente utilizados, os valores de fator de torque (k) normalmente utilizados são mostrados na tabela abaixo:
Uma faixa genérica do Fator de Torque desejado pode estar compreendida entre: 0,08 a 0,18. Os elementos de fixação (metálicos) podem receber vários revestimentos químicos para incrementar a proteção anticorrosiva e mecânica, conforme exigências estabelecidas, principalmente, aqueles destinados às indústrias automotivas e outras de mesma importância. Dentre estes recobrimentos podemos citar:
- Zincagem eletrolítica passivada – Zn/Ni, Zn/Fe e, Zn/Co;
- Cádmio (Cadmiação) – Com tendências de ser substituído para Zn/Ni (Indústria aeroespacial e petrolífera);
- Camadas organometálicas – zinc flakes;
- Fosfatos de zinco/de manganês/e semi amorfo.
A importância das camadas de fosfatos nos elementos de fixação, especialmente aqueles destinados a indústria automotiva e petroleira
Sua fabricação começa com a fosfatização do ‘fio máquina’ e calibração (Figuras 1, 2 e 3).
Após o processo de fosfatização e calibração, são realizados, em uma 1ª etapa, a fabricação dos parafusos, porcas, etc., através de conformações a frio em máquinas (prensas) adequadas, auxiliadas por óleos lubrificantes especiais. Na 2ª etapa, esses elementos de fixação passam por processos de usinagem e tratamentos térmicos específicos.
Após a fabricação desses elementos de fixação, vamos destacar alguns tipos de camadas de conversão, muito utilizadas como acabamento. Conforme exigências de cada indústria, e em conjunto com óleos protetivos ou ceras adequadas e deslizantes, graus de medição no coeficiente de atrito, ‘Torque Tension’, específicos, confere proteção anticorrosiva:
- Fosfato de zinco;
- Fosfato de manganês;
- Fosfato de zinco/cálcio - Semi amorfo.
A reação de formação destas camadas pode ser descrita genericamente, conforme abaixo: 3M(H2PO4)2 + xH3PO4+ (4+x)Fe? M3(PO4)2?+ (4+x)FePO4+ 3/2(4+x)H2
Camada depositada Onde: M = Zn, Ca, Mn, Fe etc. Pode-se oxidar o H2 que se liberta através da adição de aceleradores despolarizantes, tais como: nitratos, nitritos, peróxidos cloratos, etc. para acelerar a reação para direita.
Faixa de massa depositada sobre a superfície ferrosa dependendo da liga do aço:
- Fosfato de zinco = De 7 até 20 g/m²
- Fosfato de manganês = De 10 a 25 g/m²
- Fosfato de zinco/cálcio – Semi amorfo = De 2,0 a 4,0 g/m²
Fotos padrão em MEV dos tipos de camada acima descritas bem como sua composição na superfície metálica (EDS):
Considerações finais
O intuito desta Matéria Técnica é informar, de uma maneira resumida: Finalidade, Recobrimentos Químicos empregados (em especial os Fosfatos) e os Aspectos Mecânicos a serem atingidos, sem o aprofundamento em detalhes técnicos específicos para cada componente e sua aplicação.
Principais Referências
SENAI - Artigos técnicos publicados
Publicações da Metalac Sorocaba-SP.
Biblioteca ‘Quimidream’
Anuar Gazal
Formação:
- Técnico em Química pelo Liceu Eduardo Prado - 1971
- Licenciatura e Bacharelado em Química pela Universidade Oswaldo Cruz - 1979
Experiência Profissional:
- Laboratório Químico - Squibb Farmacêutica (1971-74)
- Laboratório Químico (desenvolvimento de produtos) e Assistência Técnica Comercial - ICI Brasil (1975-79)
- Sócio - Proprietário - Diretor Técnico - Quimidream Ltda (1979-2002)
- Consultor Técnico especializado em tratamento de superfícies metálicas – SurTec do Brasil (2002-15)
- Consultor Técnico Comercial - Quimidream Ltda (2015- até o momento)